Bi-directional AGV
Creform has designed and built an AGV to transport heavy frames for an automotive assembly operation.
The Creform model HA-B Bi-directional AGV, built with fabricated steel for strength and durability, measures approximately 80″ L x 28″ W x 30″ T.
The unit is a bi-directional AGV with Creform bolt-on drive units. Each end of the AGV follows the guidepath independently to ensure accurate and repeatable tracking. The dual drive wheels also give this AGV high load capacity and the ability to travel laterally, ideal for space restrictive areas and to allow the AGV to side shift into an interface position either for an automated lift, or personnel. The unit provides a 90° or 180° spin turn.
All features ensure repeatable alignment to consistently transfer loads. It can be loaded and unloaded by a forklift and has a frame detecting proximity sensors included for added protection. With powered engage/disengage to raise/lower drive wheels so that when the drive wheels are raised, the AGV can be repositioned by an associate.
The unit can travel at speeds up to 50 M/min. and has a load capacity of 4400 lb. (2000 kg). Creform AGVs provide a 50-course programming, 128 command capability using HMI screen located at one end of the AGV.
This unit includes I/O monitoring, course programming, error messages and error log and has an electro-mechanical emergency and parking braking system and is powered by 24V batteries. It reads floor mounted RFID tags for position feedback as well as command tapes adjacent to the magnetic tape guidepath.
- Onboard radio equipment helps maintain contact with the plant traffic control system.
The AGV route features ten stops and runs two shifts per day. The vehicle stops automatically and starts when released by the traffic control system. It is part of a 20-vehicle system within an assembly line, and the PC-based traffic control system is connected to the plant’s overall production system for complete integration.
The AGV system reduces the setup costs of the line and creates easy scalability to meet increasing or decreasing demands by allowing flexibility and adaptation in operations
An opportunity charging system minimizes the need for the user to change batteries. With each circuit of the guidepath, batteries are automatically charged by just pulling into the charging stations positioned along the route. No human intervention is necessary. This provides production efficiencies of automation and safe handling.
The unit meets safety CAT3 requirements, comes with 16-view laser scanners for obstacle detection, flashing lights, E-stops and an audible warning. Features complete safety equipment. E-stop buttons at each end of the AGV are especially important because of the length. Versatile use across various industries including manufacturing, warehousing, distribution centers, and more.
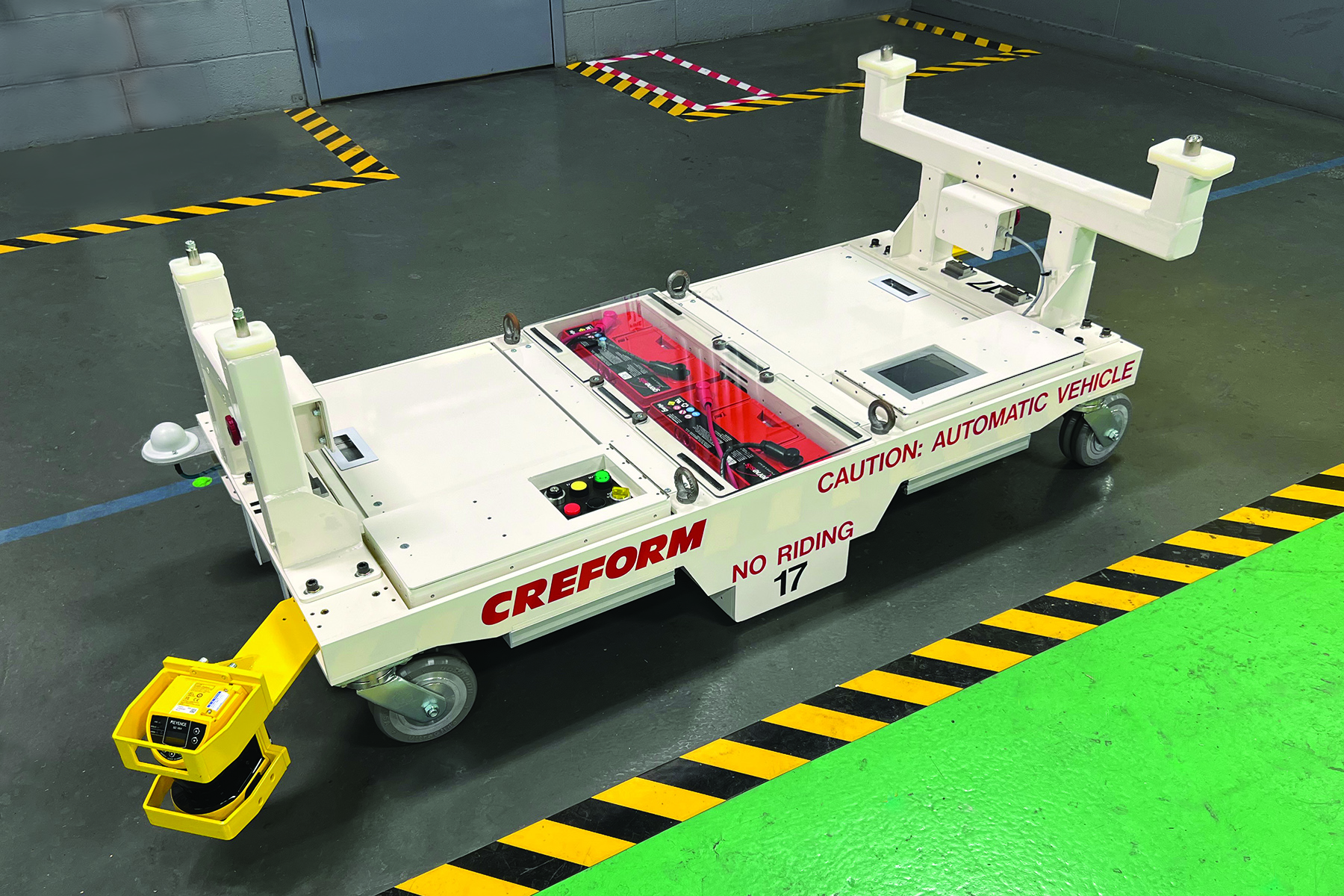
Creform HA-B, Bi-directional AGV.
The Creform system is used to create an array of material handling and efficiency enhancing devices and is a proven component in continuous improvement and lean manufacturing programs.
The company partners with customers in developing and implementing these programs.