Pintsch Bubenzer Brakes for Giant Semi-Submersible Crane Vessel
Pintsch Bubenzer installed a series of Twin Safe TS800 brakes on two 10,000-metric ton (22 million pound) capacity cranes and auxiliary hoists aboard a giant semi-submersible crane vessel (SSCV) that has recently completed its maiden voyage. The Sleipnir, part of Heerema Marine Contractors’ fleet, is self-propelled with a minimum service speed of 10 knots. It is named after Norse god Odin’s eight-legged horse.
The heavy-lift and deep-water construction vessel is over 700 ft. long and is designed to work on large offshore projects such as installing and removing jackets, topsides, deep-water foundations, moorings and other offshore structures, such as windmills. It boasts a hulking pair of revolving cranes, offering a lifting height of over 420 ft., and dual-fuel engines.
The brakes are rated for 8,000Nm (5,900 ft-lb); typically for this same motor frame size Pintsch Bubenzer’s standard brakes’ max torque is 5,200 Nm (3,800 ft-lb), thus, this design provides about a 35% boost in torque. Further, each brake presents IP67 submersible rated protection.
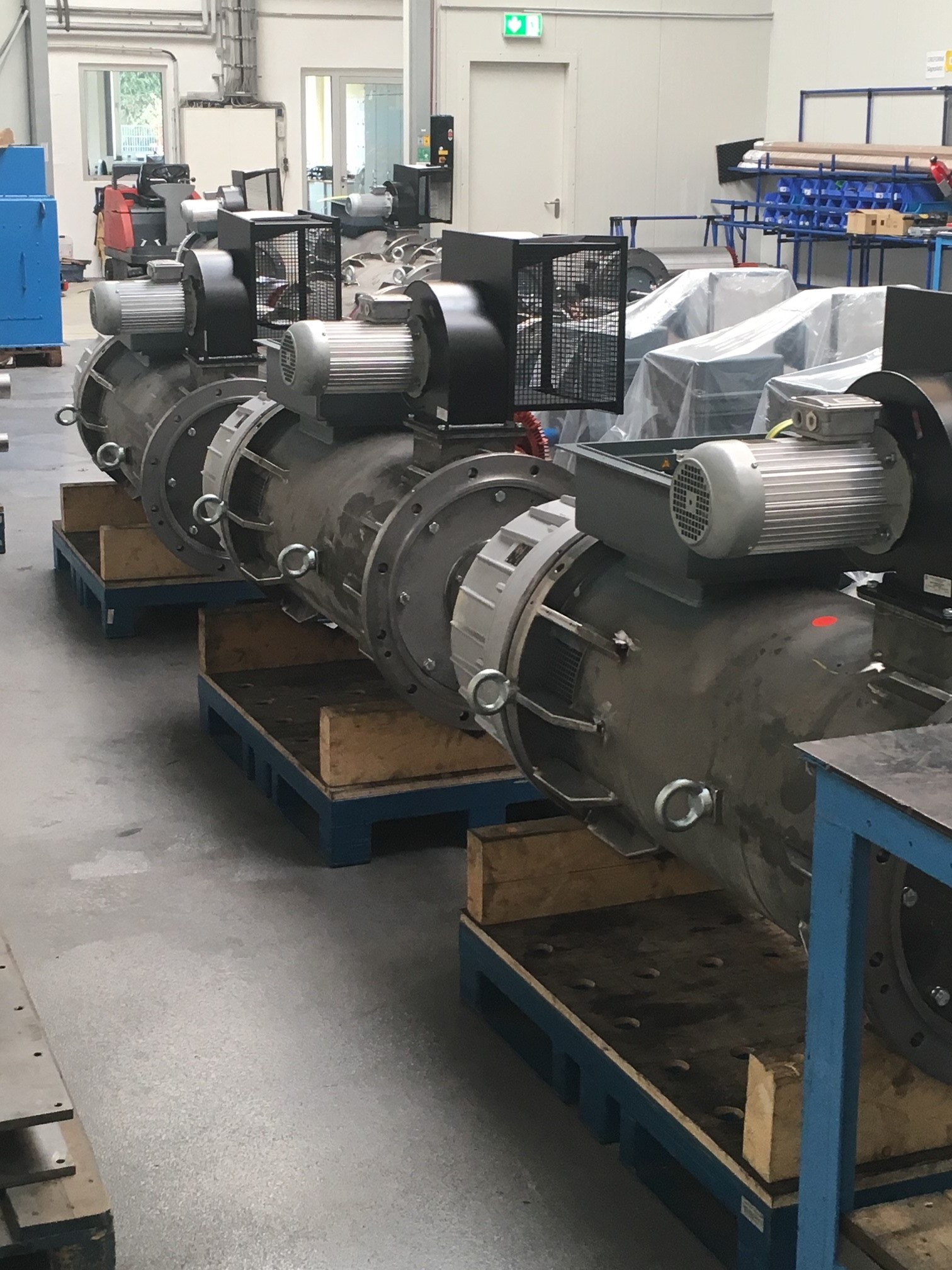
The brakes during installation at the motor factory prior to testing.
Pintsch Bubenzer, a manufacturer of a variety of high performance disc and drum brakes for severe duty applications, based the TS800 product to some extent on the success of the KFB and SFB product lines, but it stands alone due to its dual disc design. In layman’s terms, ‘twin’ refers to the two-friction disc arrangement; each disc has two friction surfaces, creating a quad surface break. ‘Safe’ refers to the failsafe design of the break, which is spring set and electrically released. Practically, this means in the event of a loss of power the brake will always be set in a safe mode. The Twin Safe range offers six different brake sizes from 2,000 Nm to 20,000 Nm.
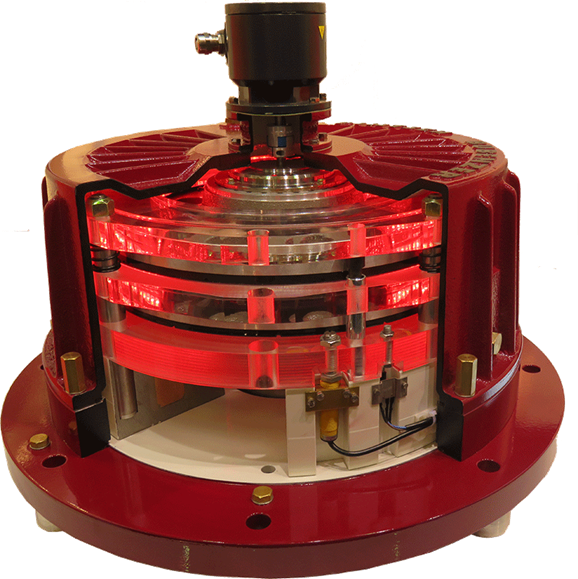
A cutaway model of the Twin Safe TS800 brake.
Mike Sparks, regional sales manager at Pintsch Bubenzer USA LLC, said: “All industries are trying to get larger to be more cost effective and we need to align our manufacturing capability and technologies with that trend. André Neth [global manager for this product] and his team are pioneering the brakes marketplace accordingly. The port industry continues to grow and the reason that this vessel was created was due to larger rig platforms being designed. The cranes were also made large to increase the amount of deck space available on the vessel since they are able to conduct the work that is usually done by three or more cranes.”
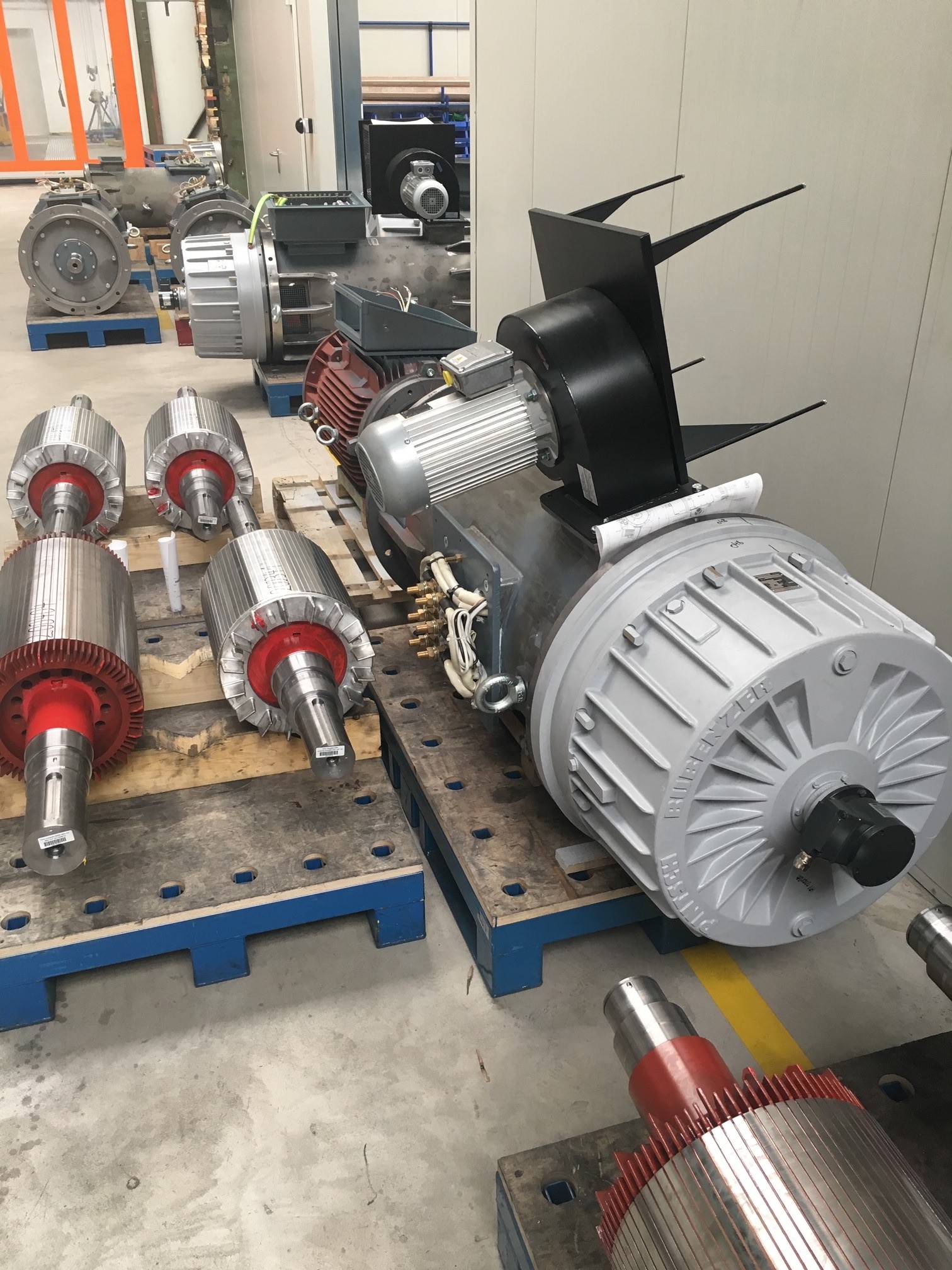
The tachometer / encoder mounted via supplied preparations.
As Neth acknowledged, the product was primarily launched to gain access to offshore projects where larger torque is required in a small package. It took six months to develop the brake based on customer requirements, which centered on a need for a high torque solution to mount onto a smaller than typical motor flange for this torque requirement. The TS800 can be supplied for a standard A660-1 or an A800 flange; as well as be adapted to the appropriate NEMA flange. The general outside diameter (OD) is 660mm (26”) or 800mm (31.5”) depending on the flange with a height of 406mm (16”).
Inevitably, extensive testing took place prior to delivery and installation. Typical testing on such a brake will involve emergency stop scenarios, multiple stop scenarios, full load stop scenarios, and high cycle testing to ensure the brake can handle day-to-day operations. Sparks reiterated, “The goal of testing is to ensure that the brake will stop the load in a worst case scenario.”
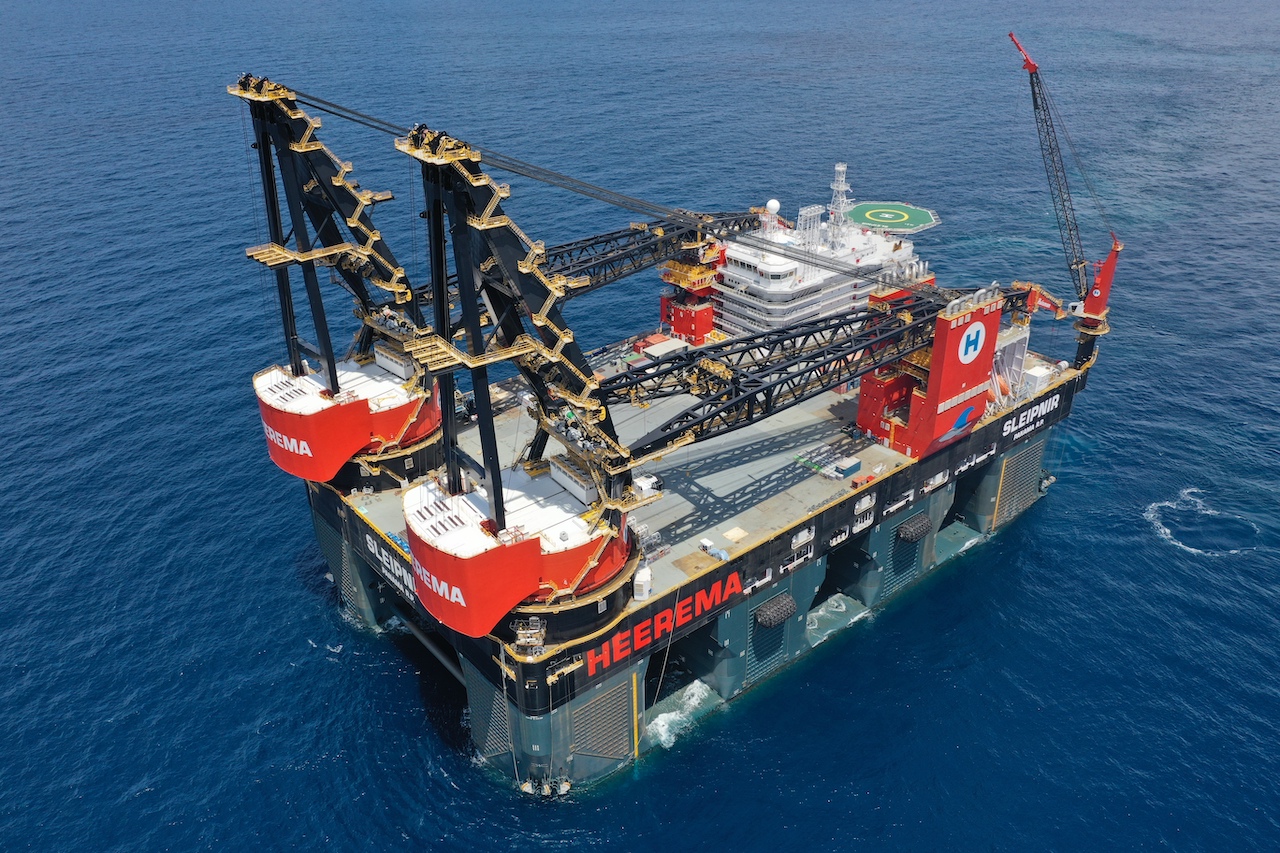
Pintsch Bubenzer installed Twin Safe TS800 brakes on the main and auxiliary hoisting drive systems on the SSCV.
He added: “The [Twin Safe] brake is suitable for a multitude of offshore and port systems due to the IP67 rating, as well as general high speed applications, dynamic braking applications in general industry, and applications that have high torque requirements with limited space. It would mount either directly onto the non-drive end of a motor or onto an accessory port of a gearbox. We also see that in most of the applications where this brake is utilized a tachometer/encoder is also required; we provide provisions for such mounting.”