Manitowoc, CM Labs Simulation
When The Manitowoc Company Inc. implemented a common control system across its diverse line of cranes, it recognized an opportunity to leverage simulators to support the marketing and sales program behind the initiative, as well as for operator training.
With award-winning simulation capabilities, CM Labs Simulations Inc. provides equipment manufacturers with turnkey solutions from end to end of the simulation value chain. This includes software development, controls integration, hardware engineering and installation, marketing expertise, and above all, extensive experience in protecting and showcasing the brand of leading companies with high-fidelity solutions.
Solution
As a provider of white label simulators for sales and marketing, CM Labs developed branded Manitowoc crane training simulators to capture the look, feel, and operator experience. CM Labs simulators are supporting the roll-out and adoption of Manitowoc’s Crane Control System (CCS) initiative by helping to train operators on the advantages of the control system. Sales and marketing teams are also employing the simulators to allow prospective buyers to virtually test-drive equipment.
Profile
For the past hundred years, contractors and owner-operators have put their trust in The Manitowoc Company to provide heavy lifting solutions. With manufacturing facilities throughout North America, Europe, and Asia, Manitowoc is the definition of a global giant. Much of the company’s growth is attributed to the acquisition of such popular brands as Grove, National Crane, Potain, and Shuttlelift. Manitowoc is equipped to support customers with any size of job or application, thanks to its wide variety of equipment products.
But diversity has its challenges. While multiple product lines help the company dominate market share, each product line has historically had its own engineering and design center. This created steep learning curves for operators as they encountered different Manitowoc crane models.
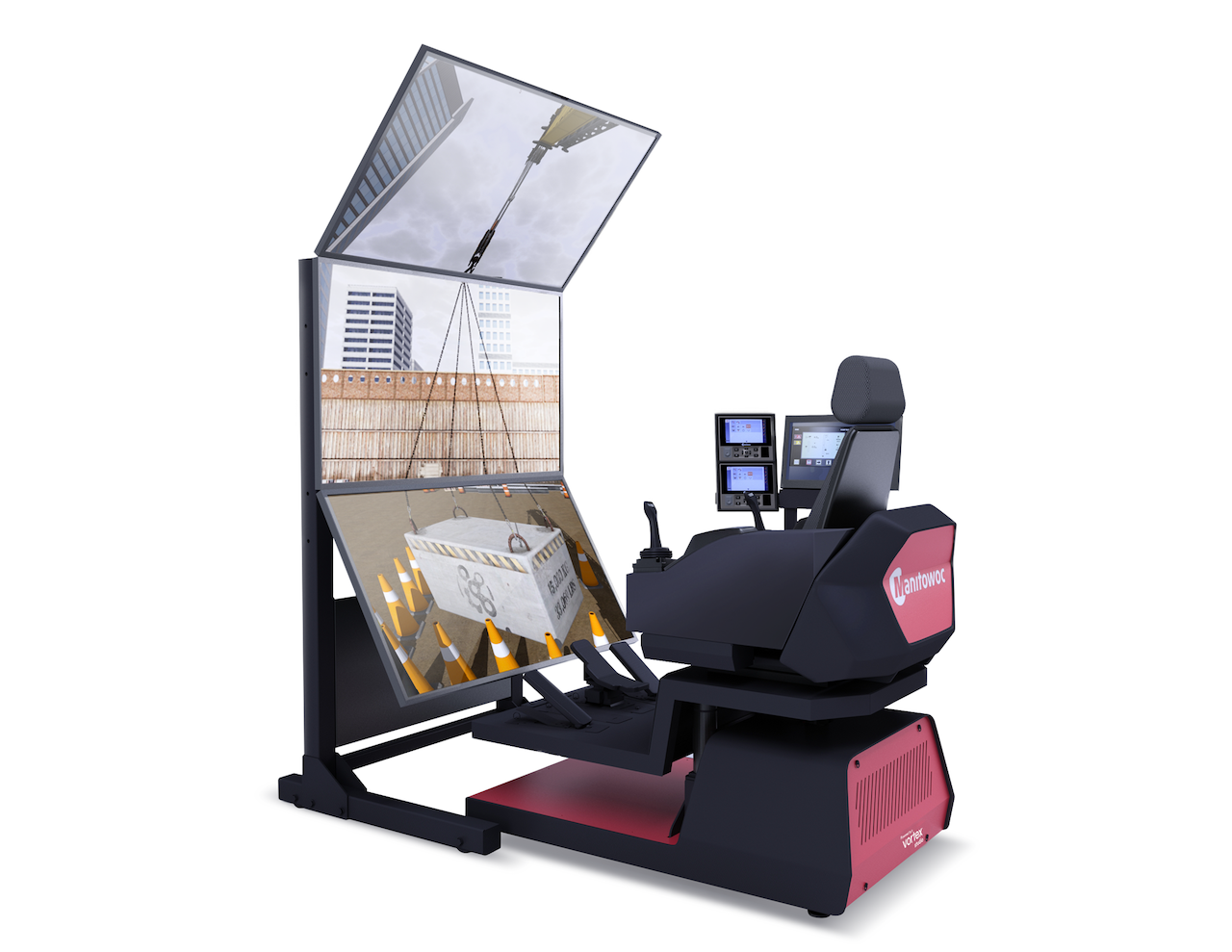
Manitowoc is taking full advantage of its CM Labs simulators.
To resolve this, an initiative was launched to standardize controls across the Manitowoc line of cranes. Found on virtually every Manitowoc crane, the Crane Control System (CCS) provides a common look and feel from an operational perspective. The objective is to provide customers with equipment usage flexibility by reducing much of the training normally required to operate an unfamiliar crane.
“With the CCS, regardless of which model you’re talking about, control inputs are very similar,” explained John Alexander, Director of Service, Training & Telematics at Manitowoc. “For example, this allows an operator to run one of our all-terrain cranes and then jump into a rough-terrain crane and have the same functionality, feel, and control inputs.”
Another benefit lies with engineering and product development. Commonality behind the core programming language of the control system inputs, is allowing Manitowoc’s global engineering community to freely share information and make enhancements throughout product lines from both a component and control system software perspective. The result of this enterprise-wide collaboration is an opportunity to leverage information and best practices to advance innovation.
Speeding market adoption with training innovation
Training plays a key role in the market’s adoption of any new initiative, and CCS is no exception.
“Even twenty years ago, machines were built without all of today’s sophisticated program control system inputs,” said Alexander. “Functions were straightforward and operated through lever action. But now cranes are controlled digitally, making operation more complex. What’s more, there are unique distinctions from one model to another that an operator has to be comfortable with. That’s why it’s critical to have well-trained operators in the seats of newer cranes, and the more standardization across models, the easier that becomes.”
When it comes to effective training, nothing beats hands-on interaction with physical equipment and controls invaluable. But field training with any piece of equipment – especially a crane – is costly and can be logistically impractical. Training simulators, on the other hand, offer a cost-effective alternative that is both practical and efficient.
“We had been interested in simulation-based training and impressed with CM Labs technology for a long time,” Alexander said. “Prior to CCS there really wasn’t the opportunity to standardize on anything related to training. But as control system commonality became more prevalent across our cranes, we recognized the opportunity to partner with CM Labs and integrate CCS controls into a training simulator.”
Manitowoc is taking full advantage of its CM Labs simulators. Whereas physical machine training can be limited by time, space, or cost, simulators are always available to provide multiple trainees with ample hands-on experience.
Training can also be adapted to the unique requirements and experience of each operator. A journeyman may require just a quick tutorial to become familiar with the inputs, while a new operator will require considerably more training time.
In addition, the ability to sell branded simulators to training schools has the potential to boost operator loyalty to the Manitowoc brand, thanks to the extraordinary learning experience provided by CM Labs’ simulators.
Simulation boosts sales opportunities
Manitowoc sells and supports machines directly and through its network of distributors. According to Alexander, the ease of use of the CCS, from both an operator and technician perspective, has become a big selling point. These and other features are clearly demonstrated through the CM Labs simulators.
In fact, when it comes to making a sale, nothing beats the opportunity to put prospective customers at the controls. This is where key features and the innovation that’s unique to the equipment really shine.
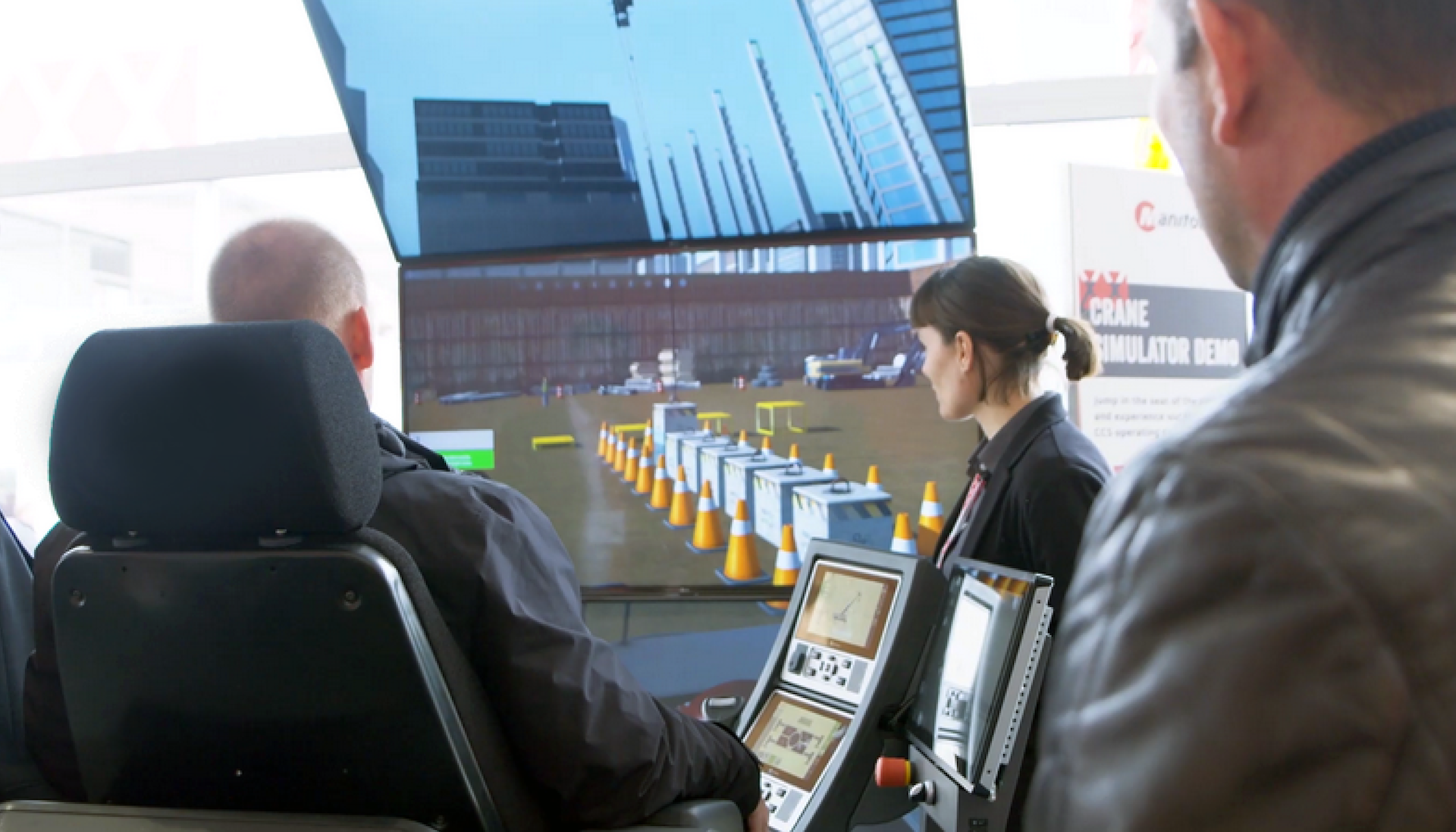
Training simulators offer a cost-effective alternative that is both practical and efficient.
At the same time, tradeshows and events offer a unique opportunity to showcase equipment to a broad range of buyers. Through CM Labs simulators, Manitowoc is providing an opportunity to experience their equipment right on the show floor. And the unique ability of CM Labs’ simulators to integrate with the CCS platforms enables Manitowoc to show just what the CCS can do.
“At a tradeshow we might have eight or ten cranes on the site, but there are restrictions regarding operating equipment. Even simply sitting in the cab is limited as you can only have one person on the crane at any given time” said Alexander. “With our simulator we can have six, eight, ten or more people watching what’s happening. This gives us a greater opportunity to showcase the benefits of our equipment and CCS technology.”
Similarly, simulators allow for demonstrating picks, swinging, and other operations that are not permitted at a show. Attendees can take the controls in hand and run the crane through its paces in a controlled, yet realistic, environment.
“Simulation allows prospective customers to go through the crane functions – options, features, etc. – just like the real thing. From a lifting perspective – how easy it is to set up the RCL, to view error codes, how easy it is to interact with the controls – all of those features can be easily demonstrated on the simulator.”
John Alexander had always been impressed with the realism and capabilities of CM Labs’ technology and the professionalism of the organization. But as a customer, he has come to appreciate the partnership even more. “I’ve found CM Labs to offer a strong product backed by a good technical group of people. The responsiveness of the staff is amazing and their willingness to go above and beyond is really refreshing.”