Caldwell Lifter, Rotator for Telescope
The Caldwell Group Inc. has delivered a custom system for rotating a track section during manufacture of the world’s most powerful telescope.
Caldwell is one of several Rockford, Illinois businesses, including milling specialist, Ingersoll Machine Tools Inc., that is delivering various scopes of work to The Giant Magellan Telescope, an international consortium of leading research institutions. The 30-meter-class telescope, which will offer 10 times the viewing power of the famous Hubble Space Telescope, is under construction at Las Campanas Observatory in Chile’s Atacama Desert, one of the best locations on Earth to explore the heavens.
Initially, Caldwell has manufactured a lifter / rotator based on a 242,500-lbs. (110-tonne) capacity Dura-Mod Modular Spreader Beam and two 20-tonne capacity RUD ACP-Turnado swivel hoist rings. Below the beam, rotation and landing assemblies on each side of the load facilitate positioning and securement of Ingersoll’s track section. Two 85-ton capacity top shackles and two 55-ton capacity bottom shackles, also supplied by Caldwell, and lifting slings, are among other key components.
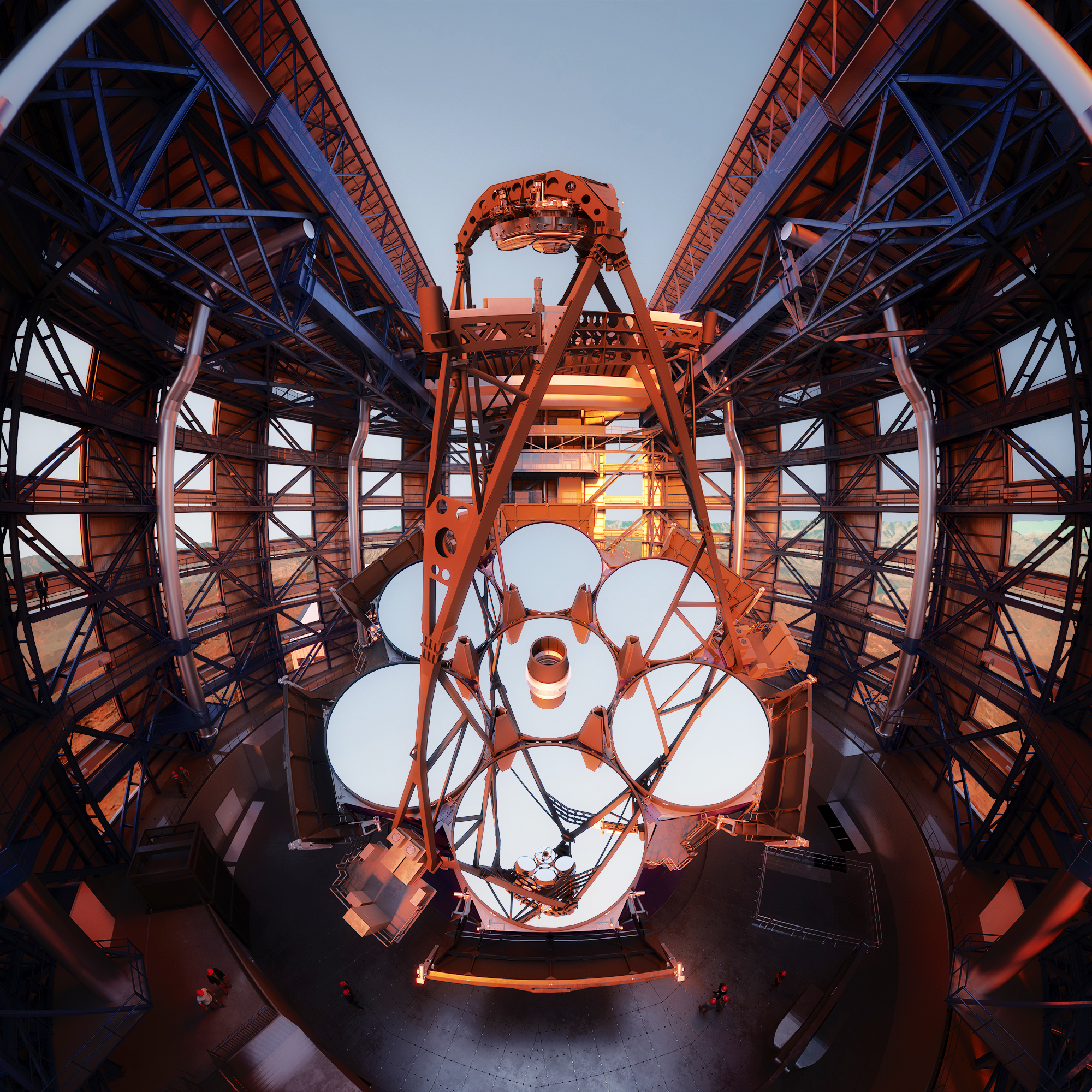
Interior rendering of the Giant Magellan Telescope, under construction at Las Campanas Observatory in Chile’s Atacama Desert. Credit Giant Magellan Telescope – GMTO Corporation.
Dan Mongan, senior sales engineer at Caldwell, said: “The track section lift / laydown system is a Dura Mod spreader beam assembly designed for maximum versatility when lifting and laying down the load. Careful installation of the rotation and landing assemblies, as well as proper selection of the upper and lower rigging assemblies, will ensure a safe lift each time it is used.”
Ingersoll Machine Tools said: “The spreader will be positioned above, and then connected to, the rotation assemblies, fastened onto the track section. The system will be raised by a hoist and adjusted by crane controls to keep the landing assemblies on blocking as the section is upended; the blocking can be adjusted as the section is lifted just clear of it in preparation for laydown. Existing holes on the load will be utilized to fasten both the rotation and landing assemblies using M24 nuts and bolts.”
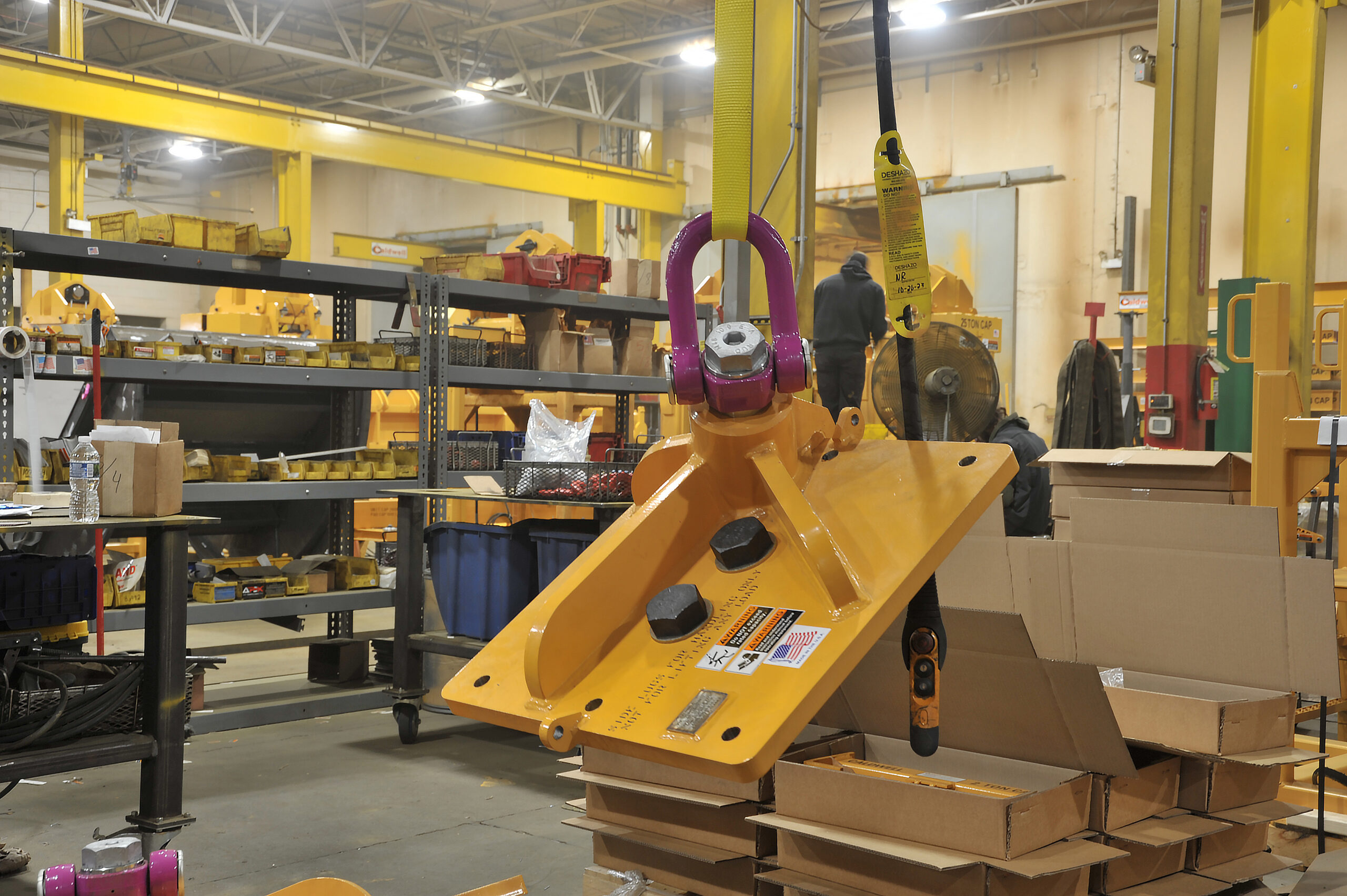
Below the beam, rotation and landing assemblies on each side of the load facilitate positioning and securement of the track section.
Jay Strong, technical sales representative at Caldwell, said: “We continue to be sought for our engineering expertise; while the Dura-Mod, hoist rings, shackles, etc., are standard components, to piece it all together using FEA [finite element analysis] is where the customization comes in. The system will initially be used to complete four lifts to flip and precision-machine both sides of the rotating track sections, but we anticipate that the wider Giant Magellan project will generate demand for additional engineering and material handling expertise from our own consortium of Rockford engineers.”
Two more Rockford businesses were also involved. Circle Boring & Machine Company was subcontracted for machining the swivel and landing assemblies after heavy structural welding at Caldwell. Powder coating was then provided by Safeway Products Inc. before final assembly with high torque specs on the hoist rings. Quality control inspections preceded packaging for shipping and loading onto an Ingersoll truck. Caldwell’s engineering team was also responsible for the product manual.
- When complete in the early 2030s, The Giant Magellan Telescope will be the largest Gregorian optical-infrared telescope in history. It will use seven of the world’s largest mirrors to see farther into deep space than ever before. Its unique design will produce the highest possible resolution of the universe over the widest field of view. It will also be the largest public-private funded science project in history.