CP&A RMGs Service for GPA
Casper, Phillips & Associates Inc. (CP&A) has completed procurement and design review services related to 10 rail-mounted gantry (RMG) cranes, manufactured by Konecranes, for Georgia Ports Authority’s (GPA) Mason Mega Rail project in Savannah.
The Port of Savannah’s Garden City Terminal was already the southeast’s busiest intermodal gateway, but GPA has implemented a series of infrastructure improvements as the port is poised to rapidly increase and expand service across an arc of inland markets, from Atlanta to Memphis, extending to St. Louis, Chicago, and the Ohio Valley.
The project allowed GPA to move cargo from vessel-to-rail in an industry-leading 24 hours; increase working tracks from eight to 18; add over 18 miles of new track to the terminal; and double the rail lift capacity to a million containers per year. It also facilitated the building of trains entirely on GPA property instead of in the residential neighborhoods, which would disrupt traffic for extended periods.
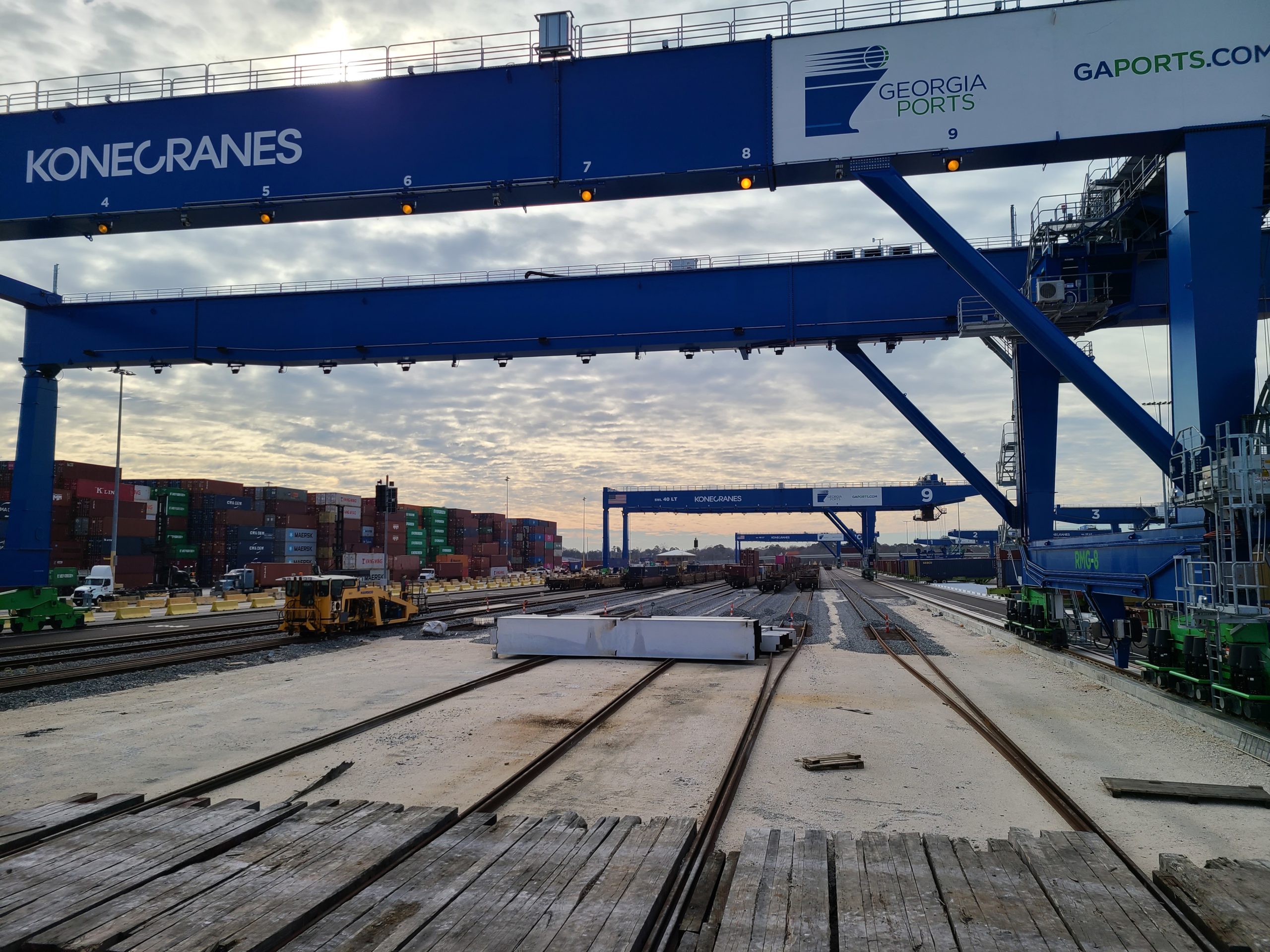
The cranes span 175 ft. over nine rail tracks.
CP&A—the company offers a wide variety of services, including procurement, specification, design, manufacturing review, modification, and accident investigation—prepared the RMG crane specifications; assisted in bid reviews; performed structural and mechanical design reviews; provided fabrication support services, including site audits to the manufacturers; and performed inspections upon delivery to GPA. The initial order was for eight cranes with a further two incorporated into the contract in time. The yard opened with two cranes in operation, long before the 10th crane was built.
The cranes, manufactured in Florida, Texas, Wisconsin, and Croatia, span 175 ft. over nine rail tracks. They have a cantilever, giving the trolley a total travel distance of 213 ft. and the cranes a total length of 245 ft. This is a long span, which thusly had to be assembled on-site. The overall width—bumper-to-bumper—is 102 ft. The Buy-America contractual agreements also presented manufacturing challenges, since normally these cranes are made more internationally.
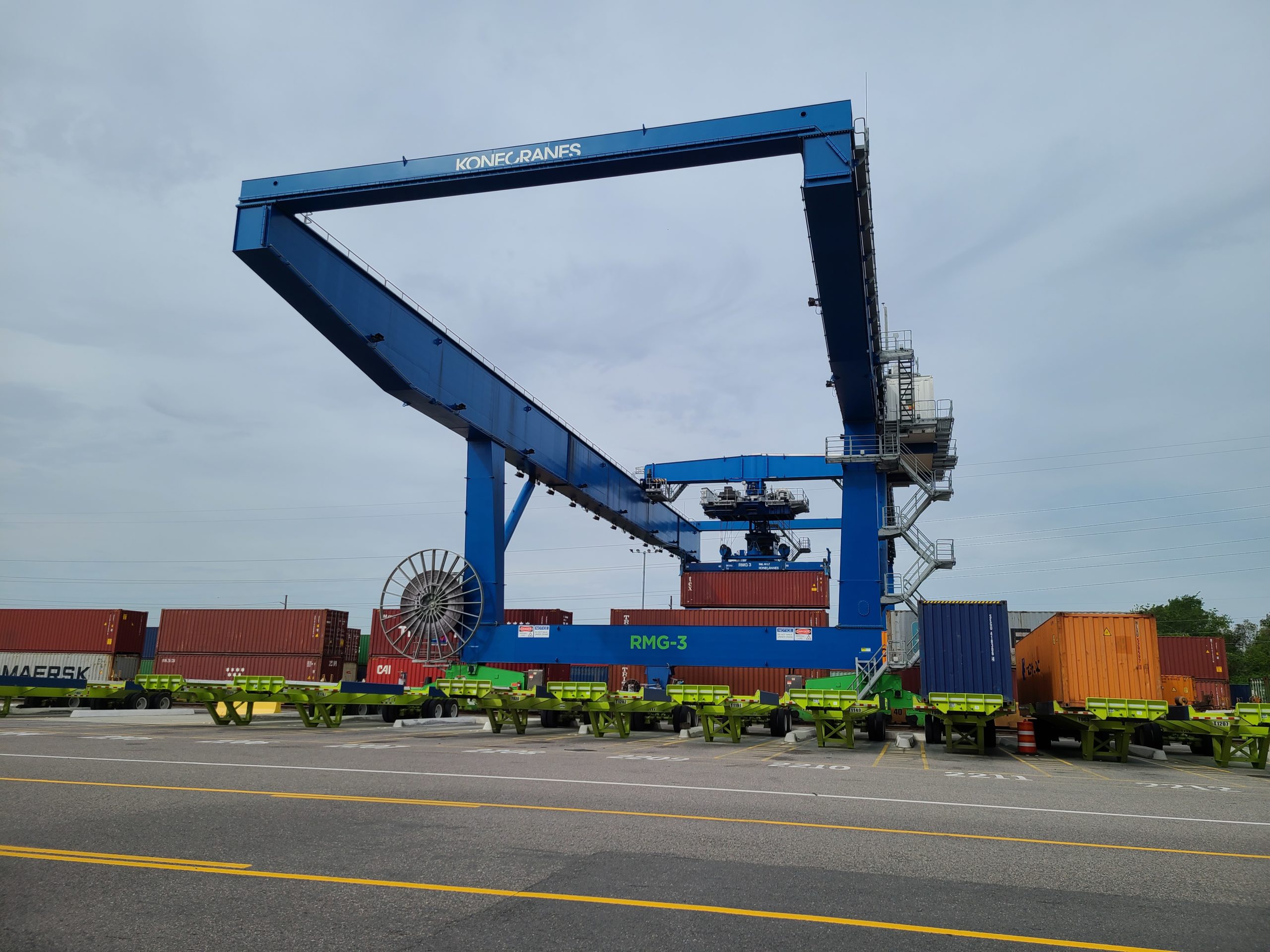
The lift heights can carry a container over a rail car stacked two containers high.
Large rail-mounted gantry cranes
Andrew Hanek, civil engineer at CP&A, detailed the scale and initial challenges.
He said: “The lift heights can carry a container over a rail car stacked two containers high [one-over-two], which puts the trolley rail at 60 ft. above ground. The trolley rotates the containers since the yard trucks are oriented 90 degrees from the rail tracks. The lifting capacity is 40 long tons [2,240 lbs.], and both the trolley and gantry can travel at 150 m/min. The crane structures were shipped all on flatbed truck, with oversized permits, and assembled on-site since the rail yard does not have access that would have permitted the cranes to arrive fully erect.”
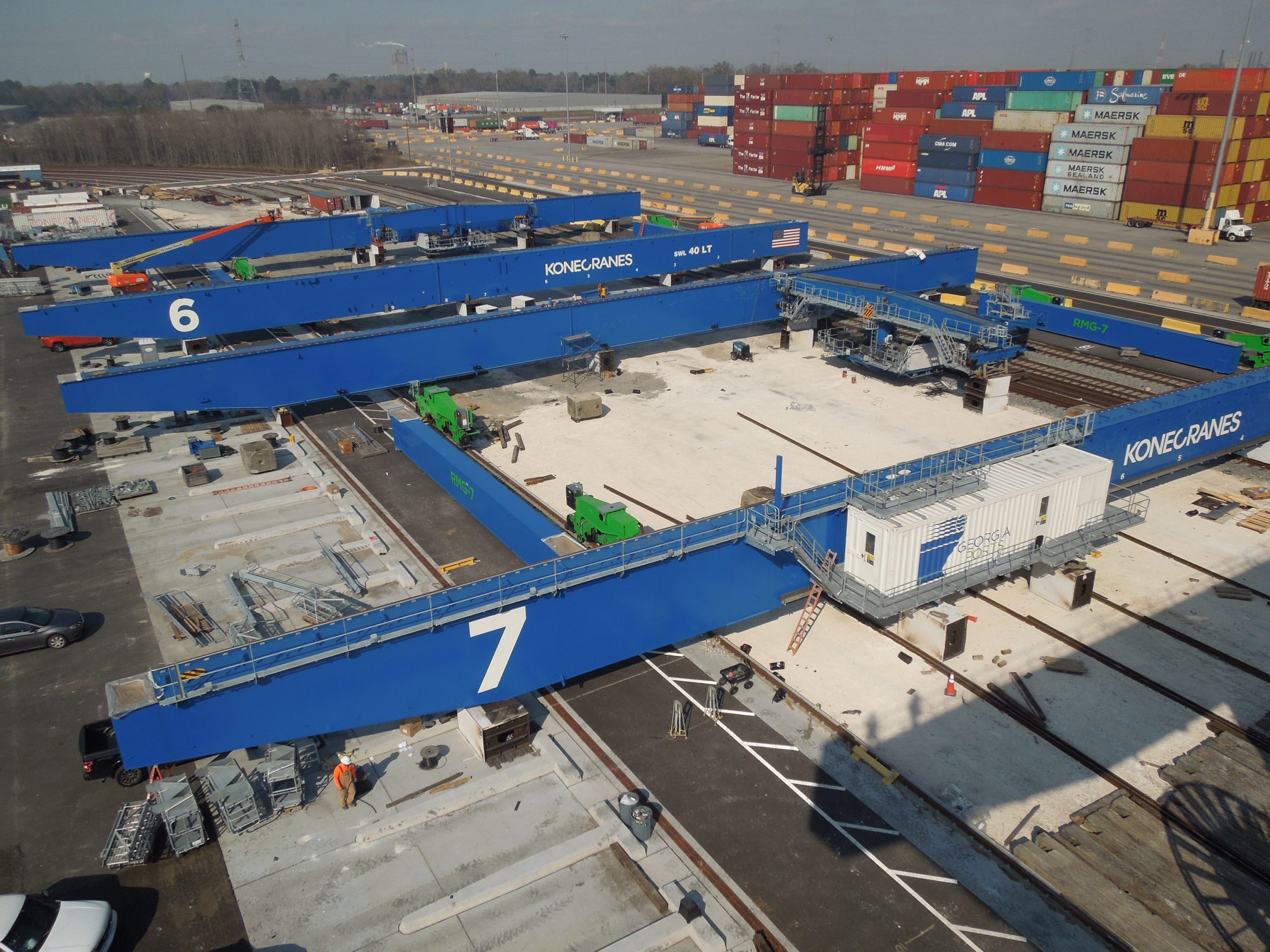
The cranes were delivered by truck and assembled in the rail yard.
Hanek explained that a design peer review involved performing independent calculations to review if the proposed crane designs met the contractual requirements. The fabrication support services provided periodic quality assurance audit checks at the manufacturing sites and review of any engineering-related issues that arose.
For such rail yards, Hanek explained that RMGs are typically specified due to their longer spans and greater speeds at traversing down the length of the train. RMGs can also be used for stacking containers in the yard but the tracks make it much more expensive to reconfigure the yard layout, and an RMG cannot cross to different container stacks. Rubber-tired gantry (RTG) cranes, meanwhile, are typically used for stacking containers in yards and can cross over from one stack to another, making them more mobile.
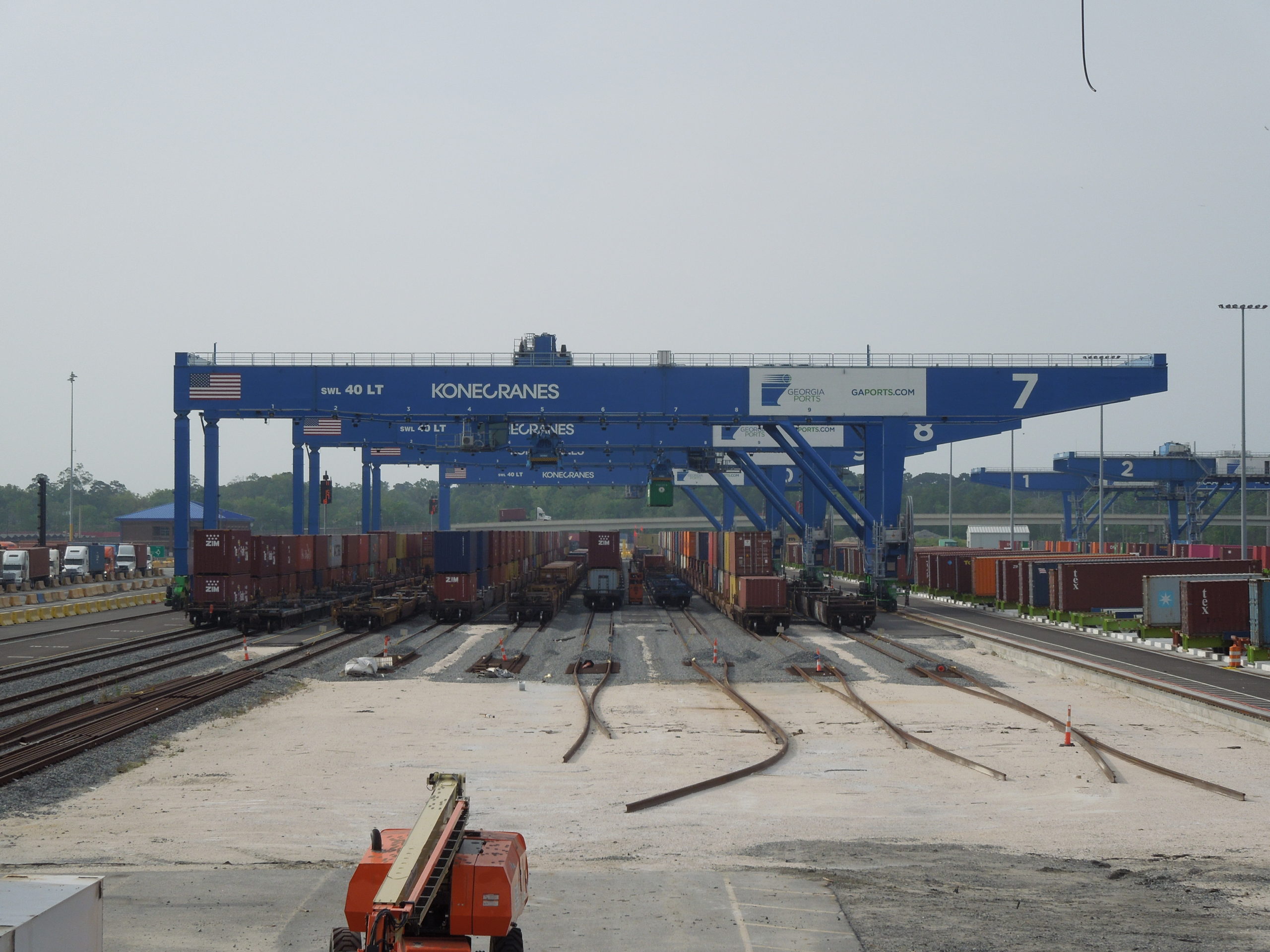
The cranes, which are numbered one to 10, have capacities of 40 long tons or 2,240 lbs.
Hanek added: “RTGs do not have to follow a rail track and their trolley movement is limited to between the legs. [An RTG] also uses rubber tires so they typically operate on concrete runways in the container yards. RMGs follow a rail track and they can be larger, and the trolley can travel outside the legs. It’s also true that RMGs typically have a higher traveling speed for both the trolley and gantry movements.”
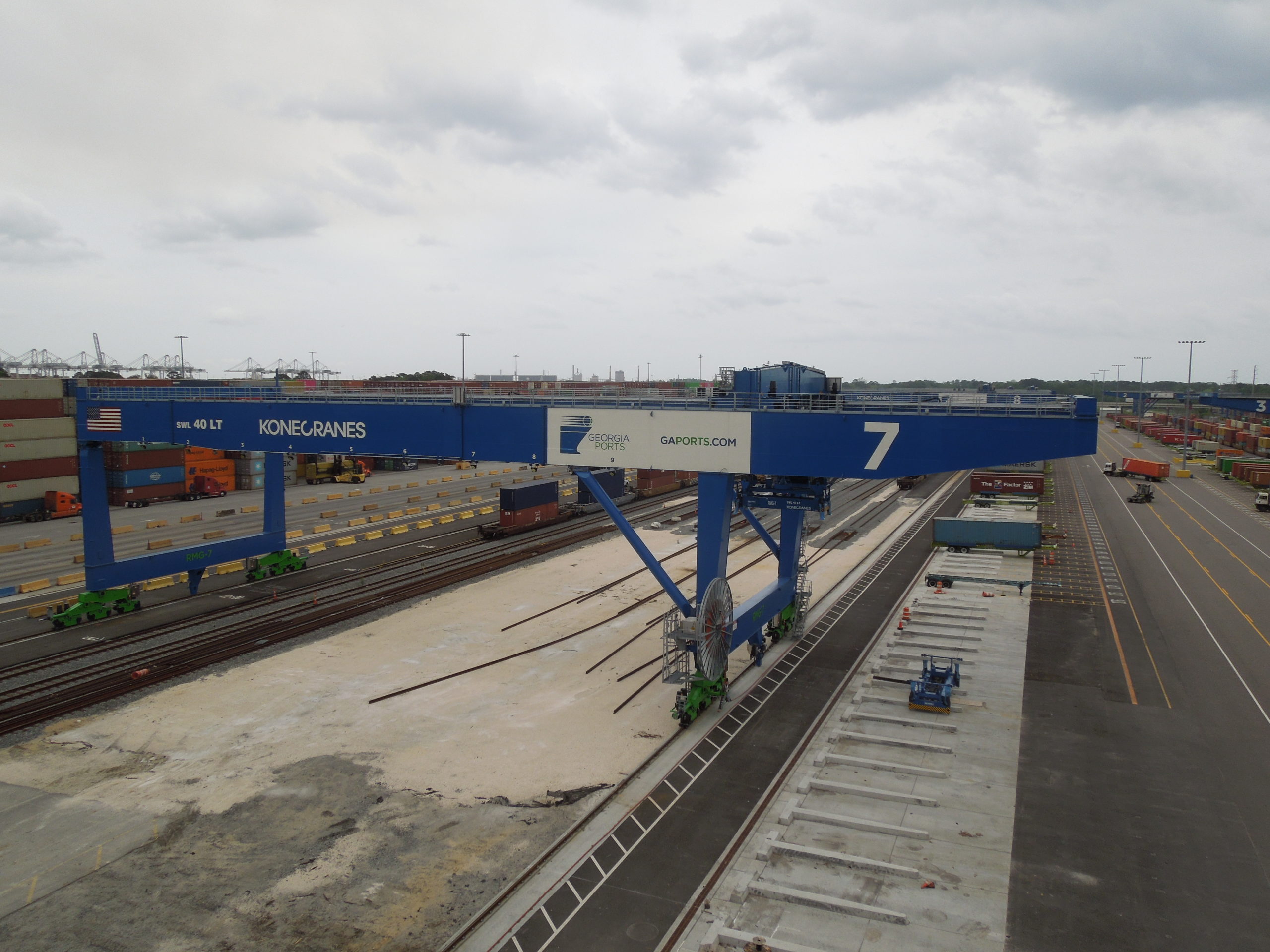
RMGs are typically specified due to their longer spans and greater speeds at traversing down the length of the train.
It is widely reported that Port of Savannah has achieved incredible growth during a global pandemic. Hanek recalled that there were initial challenges with this project, which spanned the Coronavirus era, in terms of coordination during remote working. Site visits to Croatia for the internationally built cranes were not feasible, which presented additional inspection work on those cranes once delivered to GPA.
- CP&A, which first partnered with GPA in 1988, started work on this project late in 2016 and completed its last site visit in June 2022.