Engineered Rigging Service Center
Engineered Rigging has upgraded its Equipment Service Center in Russellville, Arkansas, to offer dynamic testing and certification of hydraulic cylinders, pumps and additional high-pressure hydraulic equipment.
Equipment owners can ship their hydraulic equipment to the facility to be tested and serviced by Engineered Rigging’s experienced technicians, shown in photograph below after completing Holmatro’s dynamic testing training.
“Dynamic testing is a game changer for preventive maintenance. It optimizes equipment safety and performance and helps extend the life of your high-pressure equipment,” said Mike Beres, vice president of Engineered Rigging.
What is dynamic testing?
Dynamic testing of hydraulic equipment simulates a maximum load situation (105% of capacity) in a controlled environment to detect any internal scratches or damage to the hydraulic cylinder that could cause leaking or failure. During a dynamic test, the cylinder is pressurized for the full stroke. In contrast, static testing only pressurizes the cylinder at a set number of levels, typically three, which can allow performance issues to go undetected.
Engineered Rigging’s highly trained technicians follow a four-step testing process using Holmatro’s digital testing equipment:
- A rigorous, multipoint visual inspection of all system components, including pumps, hoses, manifold, etc.
- A dynamic test which simulates a maximum load and tests the cylinder across the entire stroke in a controlled environment.
- Repair or replacement of any worn or faulty components.
- A thorough cleaning of the equipment so it is returned looking its best and operating in top condition.
Upon passing the dynamic testing process, Engineered Rigging issues a Safety & Performance Tested Certificate, which can be added to the equipment owner’s maintenance records. View a video of a dynamic test.
“Safety is a cornerstone of our company, and we are thrilled to offer our clients an affordable and convenient way to optimize their preventive maintenance program,” said Christopher Cox, PE, president of Engineered Rigging.
In addition to digital testing, the company conducts hydraulic gantry load tests and services a range of hydraulic equipment including gantries, skidding systems, jacking systems and more. Engineered Rigging is an Authorized Enerpac Service Center and Holmatro Premium Service Partner.
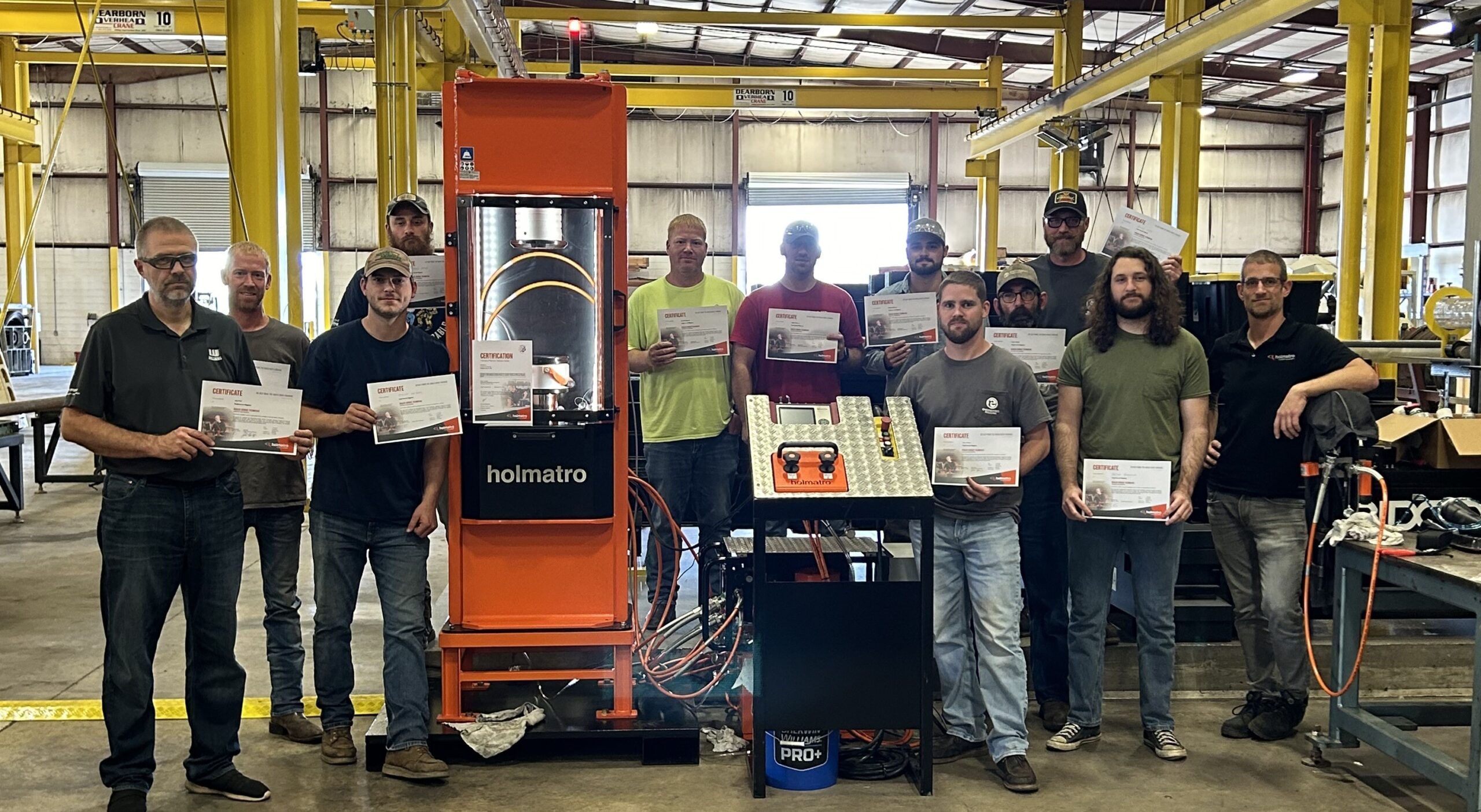
Equipment owners can ship their hydraulic equipment to the facility to be tested and serviced by Engineered Rigging’s experienced technicians.
When equipment fails or malfunctions during a project, there are numerous negative consequences. First and foremost, it puts the equipment operator at risk of serious injury. In addition, it creates a work stoppage which is costly and can lead to missed deadlines.
Upkeep reports that running a piece of equipment to the point of failure could cost up to 10 times more than a proactive maintenance program.
Furthermore, safety experts estimate that construction companies save more than $4-$6 for every $1 they spend on workplace safety. Preventive equipment maintenance is a key component of workplace safety, and it delivers an impressive return on investment.