Hirotec America Partners with OTTO Motors
Hirotec America, which supplies closure panel solutions to the automotive industry, has partnered with OTTO Motors to automate its spare parts production as part of an overall strategic goal to achieve lights-out manufacturing for 24/7 operation. The OTTO 1500 self-driving vehicle is used for automated material movement, while a Yaskawa Motoman dual-arm manipulator has been integrated onto the OTTO to pick up and dip parts in black oxide for corrosion protection.
“Hirotec is always looking for the next technology that is going to take over the industry,” noted Gary Krus, VP of Business Development at Hirotec America. “We started by looking for a platform that could make a dual-arm manipulator into a fully mobile manipulation solution. By using the OTTO 1500 with the integrated Yaskawa Motoman manipulator, we have the technology to replicate human labor. OTTO lets us test and prepare future systems to meet our corporate goals of zero operators for spare parts,” added Krus.
Hirotec America provides weld assembly equipment for original equipment manufacturers (OEMs) including GM, Fiat Chrysler Automobiles, Ford, Toyota and BMW. For close to 30 years, the division has been a pivotal part of the global Hirotec Group with more than $200 million of the $1.6 billion in worldwide sales. The company is built on the K2 philosophy of working towards continuous improvements (kaizen) and revolutionary changes in technology and process (kaikaku).
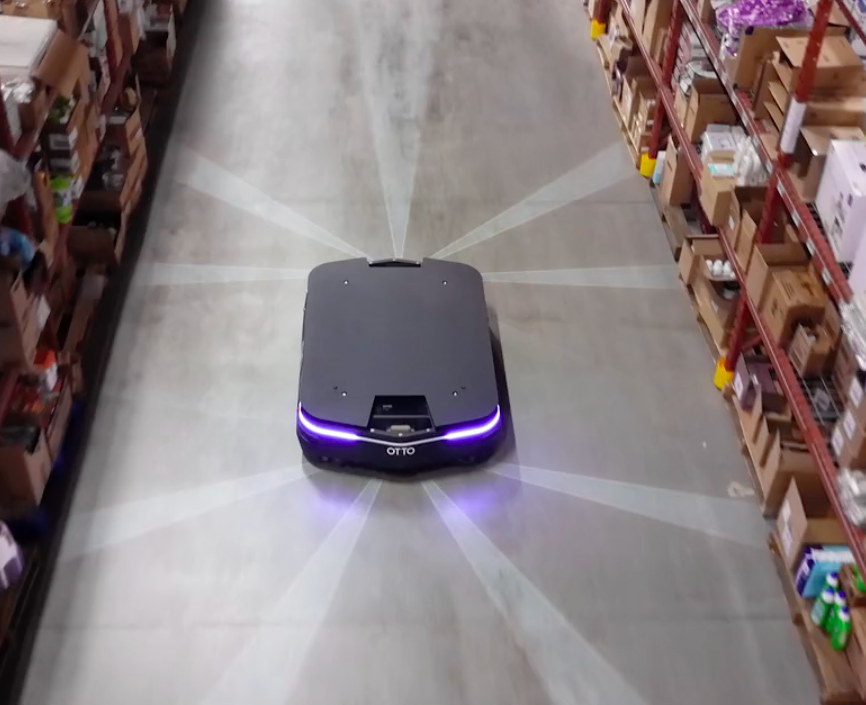
OTTO 1500 maintains a map of the space in its memory and uses visual reference points to always know its position.
“The next frontier in manufacturing is lights-out production. For so many, and for so long, this has been a vision in the distant future, but the convergence of today’s technology and manufacturing sectors is allowing this vision to become a reality. It’s innovators like Hirotec America that are leveraging new capabilities – we’re excited to be their strategic partner to make it happen,” said Matt Rendall, CEO of OTTO Motors.
The first process that was automated within Hirotec Group’s spare parts production was the black oxide process, which involves moving and dipping parts from bucket to bucket in a sequence, with specific time delays between each sequence as parts become oxidized to provide a corrosion resistant surface. Previously, the process was completed manually by whomever happened to be available from the shop floor – there was not a set operator on the line. As such, parts were prone to error and were often required to re-enter the process, significantly impacting productivity and throughput.
“We can rely on the OTTO solution to do the same thing, exactly the same way, every time. We’re seeing much more consistent parts than what we saw with our manual process. We don’t have to run the parts through multiple times anymore, which has improved our productivity in spare parts production,” said Peter Mourelatos, R&D Project Engineer at Hirotec America. “Operators can now remain focused on the valuable tasks in the shop, and not be distracted with secondary jobs like black oxide dipping.”
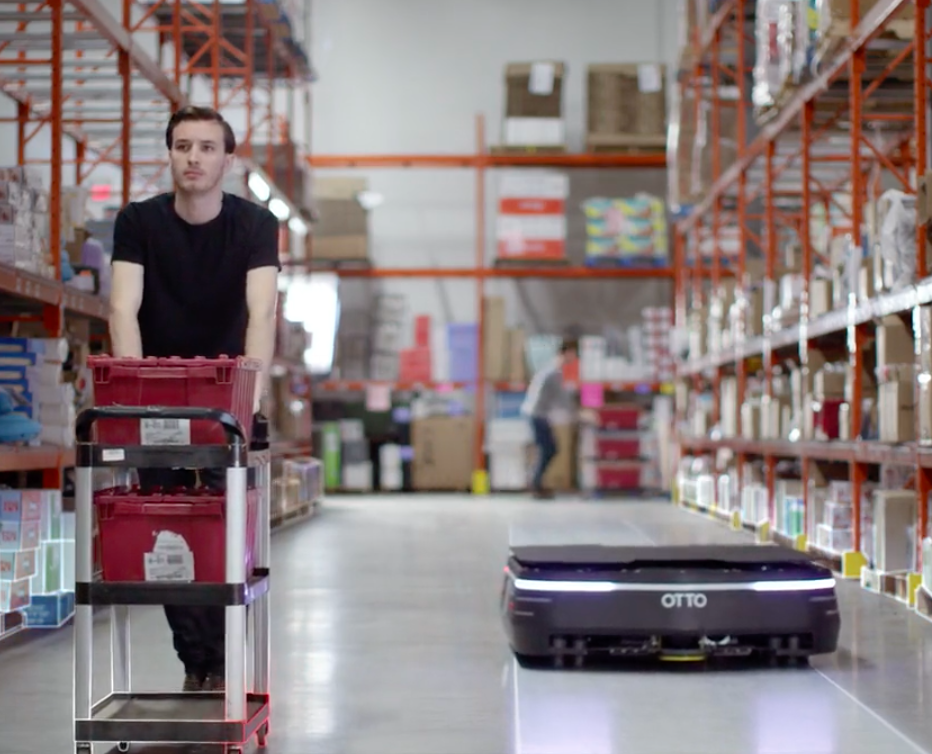
OTTO 15OO navigates spaces just like a person does.
“We’ve successfully implemented mobile manipulation at our site, and I can see the OTTO vehicle being used by Hirotec operations globally. It’s just the beginning for us as we work towards our goal of lights-out manufacturing with zero operators for spare parts production,” explained Mourelatos.
The OTTO 1500 self-driving vehicle is designed exclusively for material transport in industrial settings and can be integrated with manipulators to provide end-to-end solutions. The vehicles combine the reliability of an AGV, efficiency of a conveyor and flexibility of human decision-making by using advanced sensors and artificial intelligence.
OTTO offers flexible automation and does not require fixed infrastructure (no beacons, magnetic tape or pre-defined laser paths). Each vehicle can operate 24/7 by using opportunity charging technology to autonomously visit its charger for frequent, rapid charges between missions.
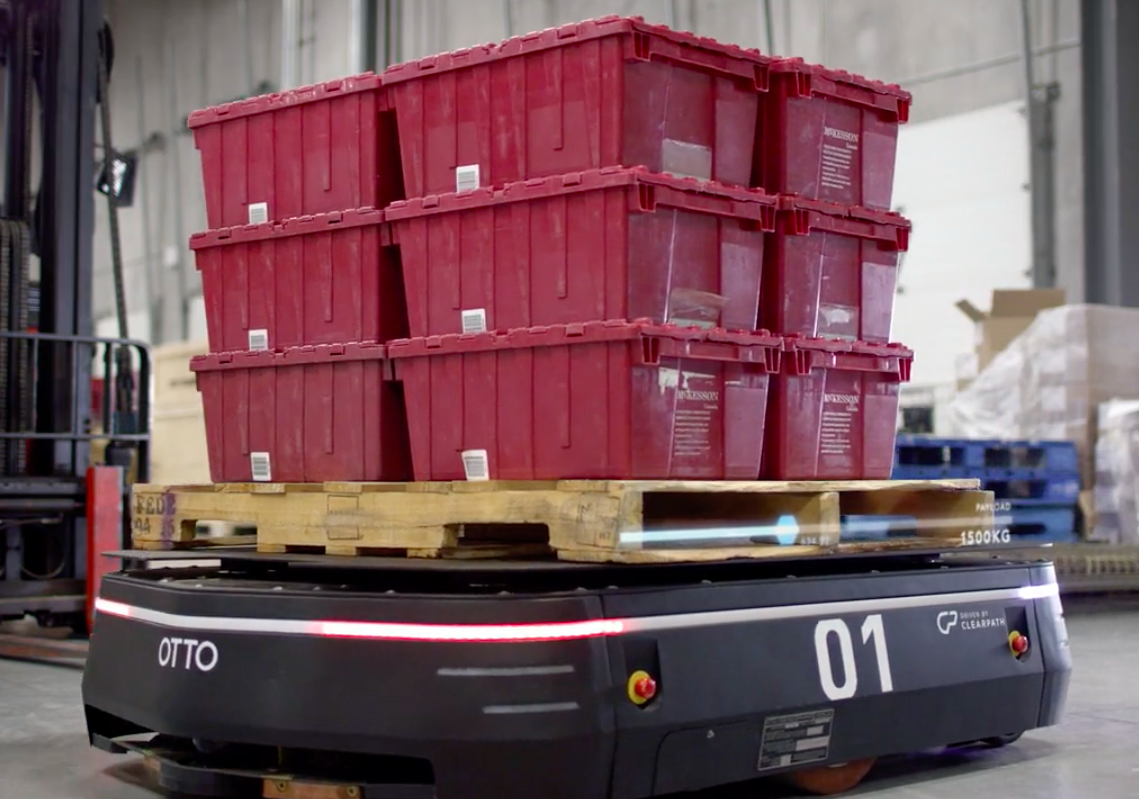
No guides, infrastructure, or predefined paths required.
OTTO self-driving vehicles will be showcased at industry’s most innovative event, Drive Manufacturing Summit, Oct 2-4, 2017. This unconventional conference will bring 350+ industry leaders together to network and determine how change can be integrated back into their facilities.