Konecranes Communicates Safety Features
Konecranes proprietary safety features are raising awareness about the value of improving the safety for inexperienced or infrequent operators when purchasing an overhead crane.
Designed with your safety in mind. That’s the new message that Konecranes, overhead crane design and operator of the world’s largest crane service network, is communicating to the overhead crane industry. This concept is the driver behind the company’s current outreach to educate crane buyers about the real value that a safer crane can bring to their operation.
An analysis by the Konecranes Training Institute of OSHA-reported crane incidents provides a compelling background for this initiative. A study tracking 249 incidents over a 10-year period showed that the average cost to an employer from a major crane-related injury was $200,000. A crane-related fatality cost an average of $4 million.
The study identified being crushed by the load (caused by load swing, load drop or by an unstable load being placed and then immediately falling over) as the primary cause of these incidents. Operators being crushed by a load resulted in 33.8 percent of the fatalities and 36.8 percent of the injuries.
As a result, Konecranes is committed to educating crane buyers about how its proprietary “safe” technologies address the issue of load swing, creating a safer crane that they believe will raise the bar for all overhead crane manufacturers.
Mark Ubl, senior vice president, industrial cranes, Region Americas, compared a crane equipped with these features to what consumers currently expect from today’s automobiles.
“You wouldn’t buy an automobile today without anti-lock brakes or airbags. Once you own a car with a backup camera and sensors, you become accustomed to that margin of safety,” says Ubl. “The safety technologies that we use in our automobiles have become so commonplace that we take them for granted. A similar shift in thinking is now occurring for overhead cranes.”

Hook Centering is an innovation that was designed to automatically eliminate side pull situations and load swing caused by side pull.
Together, Konecranes Active Sway Control and Hook Centering are features that are capable of dramatically reducing the number of crane-related accidents. Both require a PLC, variable frequency drives and Konecranes proprietary software to operate.
Active Sway Control stabilizes load movements in trolley traverse and/or bridge travel directions. It modifies the operator’s speed commands so that the requested speed is reached with minimal load sway. If the rope angle exceeds a pre-set value, trolley and bridge travel motions respond to keep the load stable without swing. This system also dampens load sway generated by normal motion to help the load remain stable at all times and in all conditions, making load moving operations not only safer, but as much as 60 percent faster.
Hook Centering is an innovation that was designed to automatically eliminate side pull situations and load swing caused by side pull. Side pull occurs when the hoist lifts an object that is not directly beneath it, which can cause violent load swing. When Hook Centering is activated, the crane automatically positions the trolley and bridge over the load. At the same time, the hoisting-up movement is limited until the crane and load are vertically aligned. Then, lifting can continue normally.
“Hook Centering is one of the most important technologies offered in overhead cranes today,” says Ubl. “The average crane is 30 feet in the air or more. If the load is not centered properly, as soon as you lift, the load begins to swing. Hook Centering positions the crane directly over the hook preventing sway before it ever happens. It is exclusively available from Konecranes.”
These technologies are a small sample of what Konecranes offers to help operators work more efficiently while protecting people, products and equipment.
“Most crane operators are infrequent operators,” says Ubl. “They may be machinists or fabricators. Once they finish doing their real job they use the crane to pick up material or product and move it somewhere else. These technologies allow a part-time operator to control a load just like a pro.”
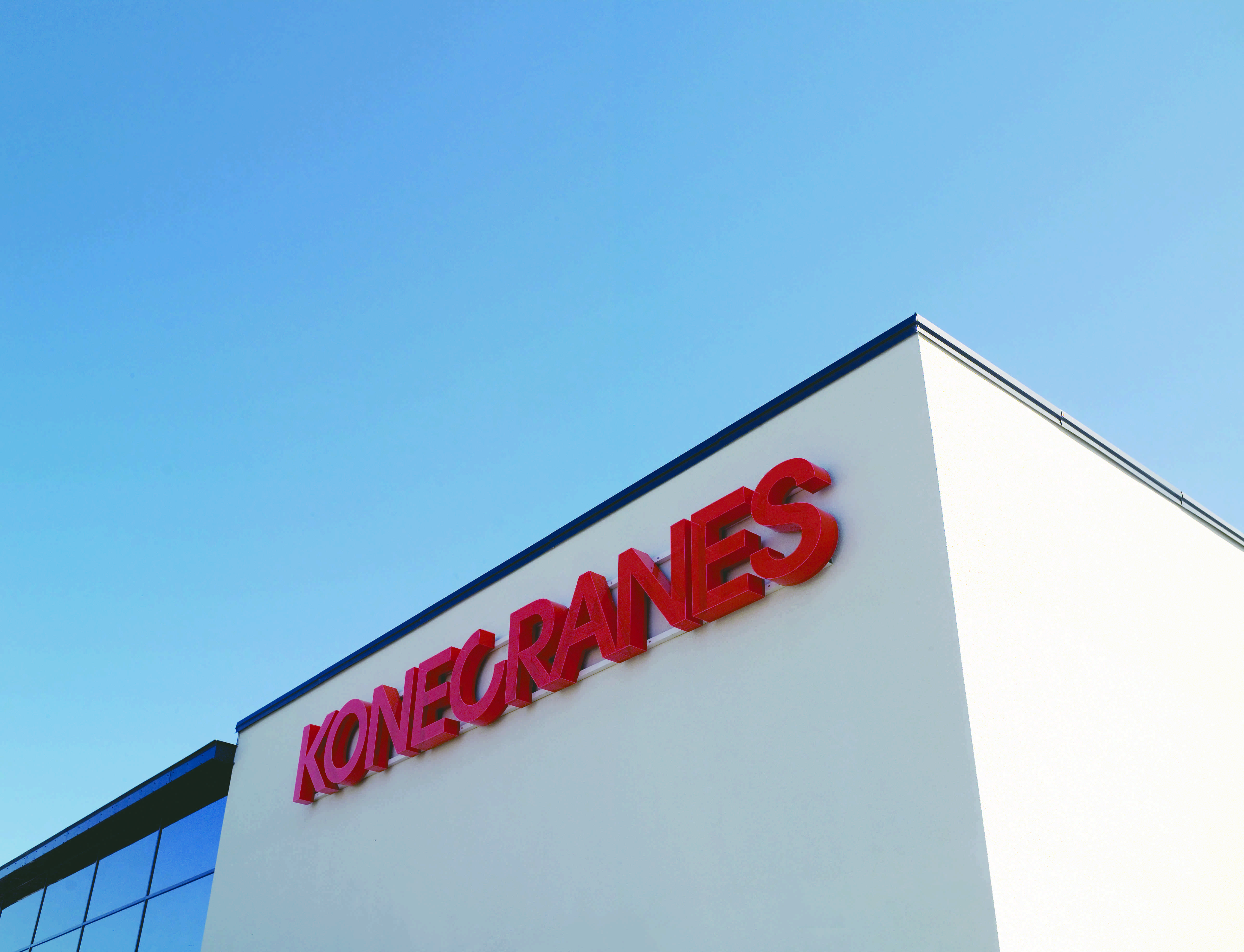
Konecranes is committed to educating crane buyers.
So, what is a safe crane worth?
According to Edward Di Cesare, director of marketing, industrial crane products for Region Americas, employers should ask themselves a couple of hard questions. What value do you put on an employee? And as a corollary, how much is your equipment worth?
“We recently visited several tool and die manufacturers, and each of their machines was valued at least a million dollars. Damage to one of those would have an enormous impact on their production schedule and their bottom line. So we finally arrive at the heart of the matter,” says Di Cesare. “Does it make good business sense to spend a few dollars more to improve safety? Of course it does.”
Mark Ubl had the final word. “Our goal is to achieve zero overhead crane incidents. We take this goal seriously as we want workers who operate cranes to return to their family at the end of each work day. That’s why we ask crane buyers to consider the suite of safety technologies available when purchasing an overhead crane.
Bottom line, if you can’t afford the technology, then you certainly can’t afford an accident,” he said. “That’s why our overhead cranes are designed with your safety in mind.”