LGH Supplies SP Load Cells for Turbine Pump Project
Construction company Pace Contracting recently completed removal and installation of three vertical turbine pumps, used in emergency flooding situations in downtown Louisville, Kentucky. Integral to the project were four 50-ton capacity Straightpoint (SP) wireless compression load cells supplied by Lifting Gear Hire (LGH).
Pace accepted a scope of work from the Metropolitan St. Louis Sewer District (MSD), which partners with 59 municipalities (co-permittees) to comply with storm-water permit requirements for the St. Louis Metropolitan Small Municipal Separate Storm Sewer System. MSD charged Pace with jacking and remounting new replacement flood pumps, having removed the old units.
LGH provided from its hire fleet the load cells along with SP software (SW-MWLC) and a rugged tablet. Pace also utilized a 10t capacity air hoist from LGH and a 12-ton hoist on a gantry crane that was permanently installed in the building above the pumps. The pump columns were designed to be installed in five sections, with a total weight of 28,350 lbs., which exceeded the capacity of the 12-ton crane.
Michael Bryant, project manager at Pace Contracting, said: “[Therefore], we had to utilize the hydraulic rams on the bottom of the pump to support the weight of four sections while the crane installed the fifth and final section on the main floor. Once that piece was installed the lower four sections were raised up, using the hydraulic rams, so the pump could be bolted together. The load cells were very useful because they helped us keep the center of gravity for the lower section of the pump centered, preventing it from tipping over.”
Dan Tobin, heavy rigging and lifting OSR at LGH, explained that two major complications on the project were caused by this offset center of gravity and the fact that the physical line of sight for the last 12 in. to 18 in. of the jacking process was lost once the pump assemblies were in place.
The offset center of gravity on the 3.5-ft. diameter structures was due to a discharge elbow midway up the suction tube assembly. As explained, the solution was to employ the load cells atop four LGH hydraulic rams, which sat on timber blocks, to weigh the 35-ft. suction tube and pump as it was assembled.
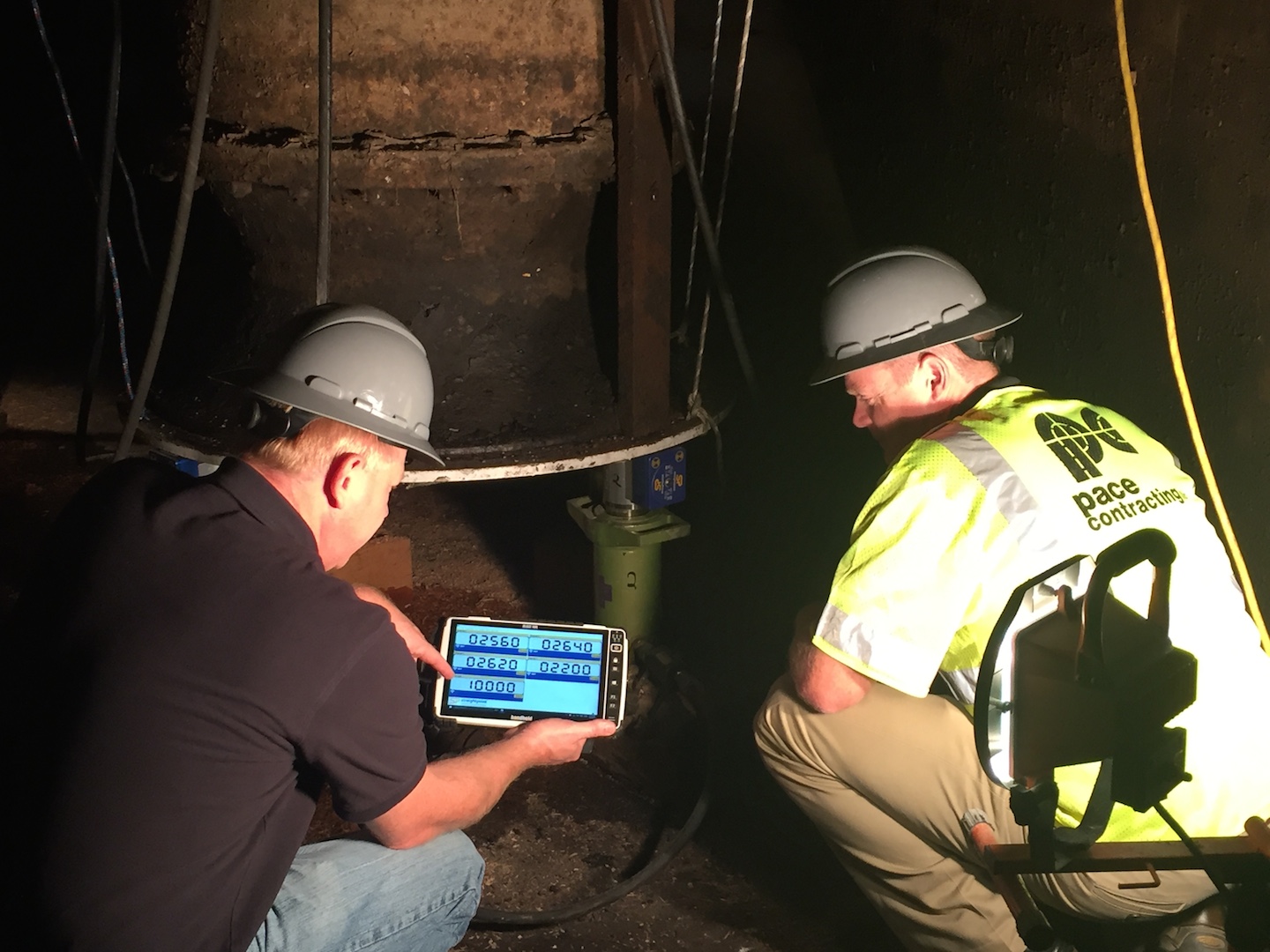
Load cell readings were taken on a rugged tablet.
“We used the tare weight mode and set the weight sensitivity scale down to 20 lbs. per jack point; we also programmed the alarm mode for additional safety,” Tobin said.
Pace safely jacked the last part of the entire assembly by using SP’s 2D center of gravity function to align the flange holes to the roof studs, despite only 0.5 in. of tolerance. Tobin said he was familiar with the concept following consultation with Wayne Wille, technical sales manager at SP, who introduced him to the ability of the product to display live, clear readings, featuring 2D center of gravity, on a handheld device.
He added: “I immediately saw the potential for new and existing LGH rental customers and this application served as a case study that we’ll use to further demonstrate that capability.”
Both operator and crew were safely out of harm’s way to complete all three jacking jobs. “The complete solution was covered by a three-week rental and saved over a week in additional labor costs,” Tobin said.
Bryant concluded: “We were satisfied with the solution presented by LGH; the SP equipment was easy to use and truly plug-and-play. We were grateful for the technology and expertise, given inherent complications with working around the two-story building in a downtown environment, whilst working 50 ft. below ground level.”