AGV for Vehicle Parts Manufacturer
Creform has designed and built a new AGV for a commercial vehicle parts manufacturer in Mexico who once again chose Creform’s expertise. The AGV tows carts holding production parts back and forth between the warehouse and the assembly area.
This project consisted of one single direction, two-ton Creform RA-B40200-CRE1 AGV drive unit. Each end of tugger, which features dual drive wheels, follows a guidepath independently and can maneuver in close quarters. It operates in a multi-shift environment and is built with heavy-duty usage in mind, but with the need to be lightweight, flexible and affordable.
The AGV is built with a sturdy steel frame and a hitch that is affixed directly to the steel frame, all designed to handle the rigors of industrial towing. The frame is designed so that the unit can be easily and safely lifted for maintenance with a forklift. In addition to towing, the AGV also features a utility load deck for misc. boxes and supplies that can ride along.
An operator interface panel is positioned atop the electrical panel and features an HMI screen with WIFI connection to off board systems that are used for vehicle position monitoring. The unit includes an RFID reader, with tags embedded in floor with unique numerical assignments, and uses the data retrieved from the floor to make routing decisions and initiate other functions such as speed and obstacle sensor view changes.
The AGV is equipped with a 24-volt system powered by two 12-volt 160AH AGM batteries on a battery tray. This tray is supported by rollers on the AGV, battery transfer cart and battery charging station. There is no need to lift the batteries. It is only necessary to roll them on low friction Creform rollers from the AGV to the battery transfer cart to charging station and vice versa.
The Creform AGV Tugger follows a peel and stick magnetic tape guidepath that is easily and quickly installed and changed depending on the need. It follows a 1000 ft. path with a long single run with multiple stopping points and a loop at either end to reverse direction. In this application, the guidepath is covered with heavy-duty protective cover tape to give the surface-mounted tape some visibility and durability. An embedded guidepath is available for high traffic areas.
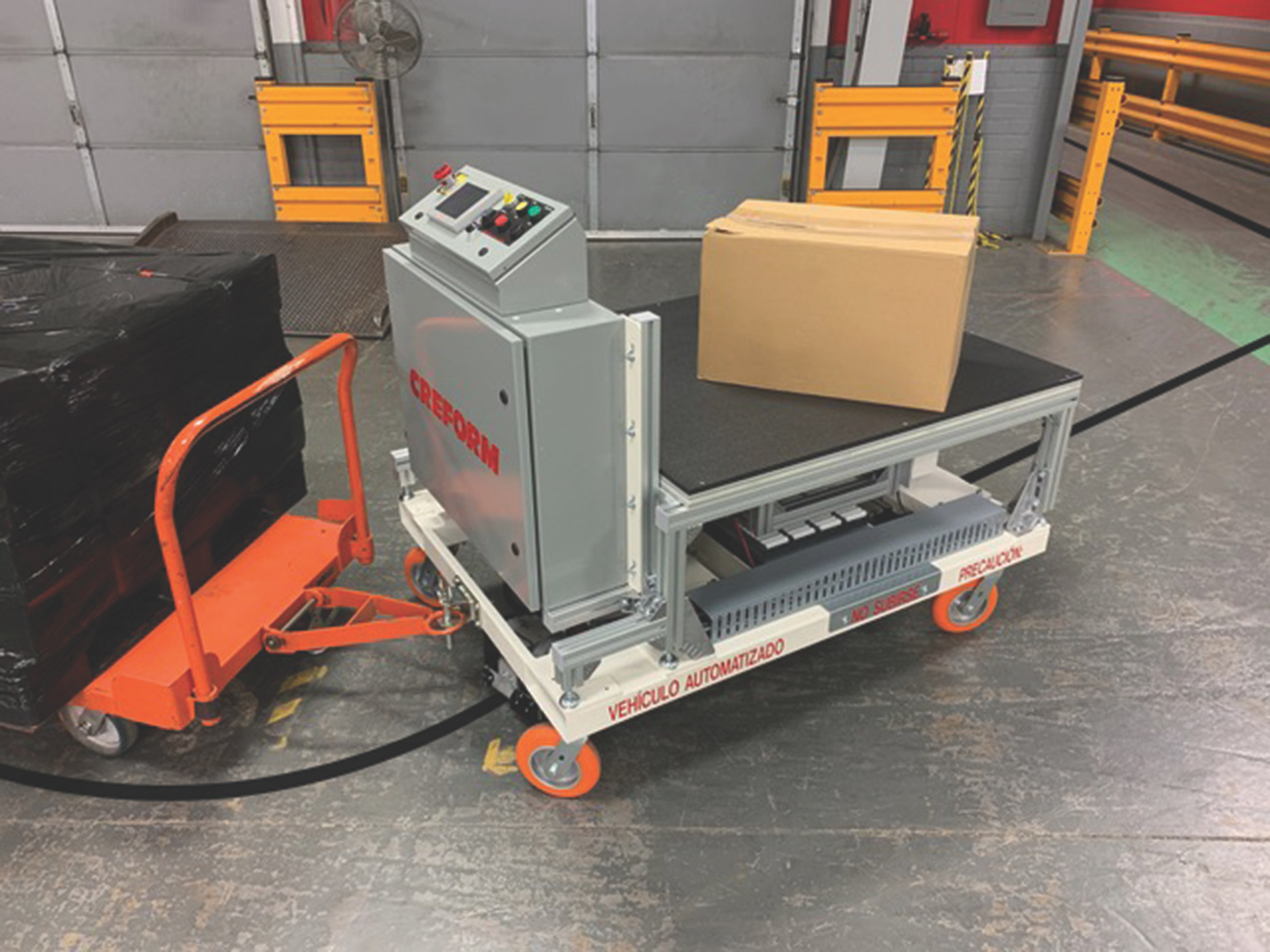
Creform one ton AGV Tugger.
Other features of the unit include PLC with HMI interface on-board controls, 50 course and 128 commands control. The AGV Tugger boasts a 4400 lb. (2000 kg) load capacity, a 240 lb. (110kg) draw bar and can travel up to 131 ft./min. (40 M/min). It has brakes for stopping and parking.
The AGV unit features a Category 3 safety system with safety equipment that includes an audible warning device, flashing light, no- contact obstacle sensor (Laser Scanner) and E-stops.
The Creform system is used to create an array of material handling and efficiency enhancing devices and is a proven component in continuous improvement and lean manufacturing programs. The company partners with customers in developing and implementing these programs.