Airpes Presents Eagle Black Box Crane Monitoring System
Barcelona, Spain-based Airpes has launched a black box product—the Eagle—that monitors and logs the hoist, trolley and bridge movements of high duty cycle overhead cranes and hoists to ensure safe lifting and use within intended parameters.
Airpes, a weighing systems and lifting equipment specialist, is presenting the Eagle system as part of its AL-series of overload devices, but it sits at the top of the portfolio, including a multi-hoist overload protector, multi anti-collision crane system, and full connection with a black box app, for download on a laptop or smartphone. The system is available with a customised black box for hoist manufacturers’ volume production.
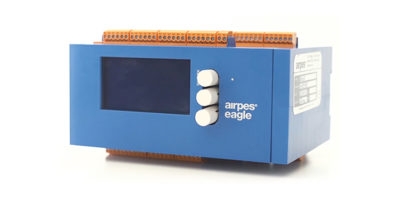
The Eagle monitors and logs the hoist, trolley and bridge movements of high duty cycle overhead cranes and hoists.
The Eagle can be installed in the control panel, usually located on the trolley or bridge, of a new electric overhead travelling (EOT) crane, or retrofitted. It is manufactured to M8 standards, a duty rating covering 20 or more lifts per hour at or near a crane’s rated capacity. This equates broadly to U.S.-based norms, Crane Manufacturers Association of America (CMAA) E / F or Hoist Manufacturers Institute (HMI) H5+ duty.
It primarily suits the Eagle to installation on cranes in medium to heavy-duty environments such as steel mills, coil processing plants, steel service centres, precast cement factories, metals production, shipyards and ports. However, it is also suitable for lifting applications where the duty cycle might be much lower, but where the load is extremely fragile and / or expensive, as is commonplace in the aerospace and nuclear industries, for example.
Tad Dunville, general manager at Airpes North America, said: “It is a multifaceted product with many features, but a holistic benefit is the input and output data it provides in relation to SWP [safe working period], which is the legally-mandated maximum run time before overhaul is required. Starts, cycle times, overloads, etc. are all calculated to provide a comprehensive overview to increase productivity and throughput for cycle-conscious customers.”
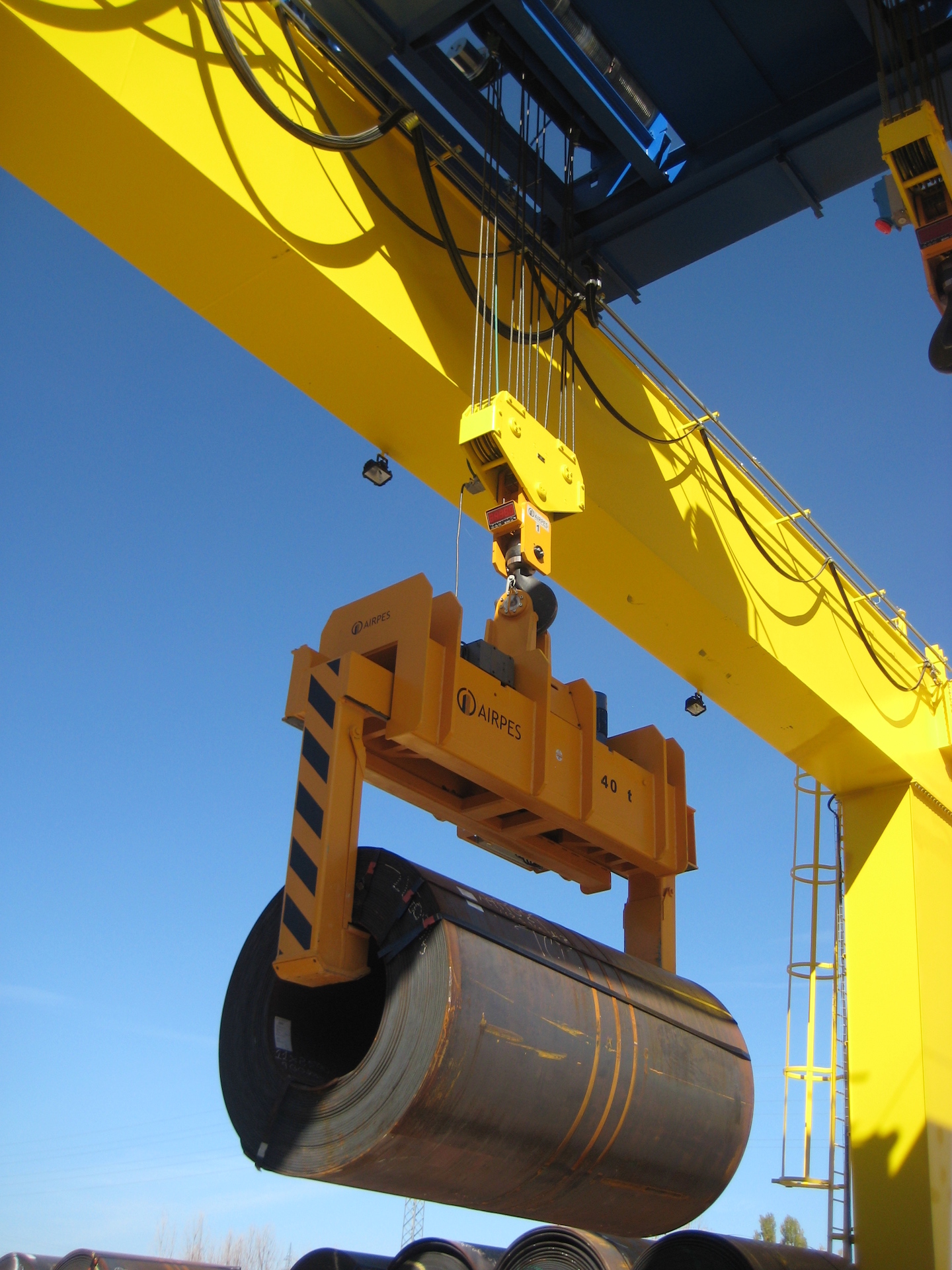
The Eagle is suited to installation on cranes in medium to heavy-duty environments such as steel mills.
While serving as an SWP controller to FEM 9.755, the Eagle can control up to four hoists and features a load limiter with 10 configurable outputs on 30 limits. It also covers 10 combinations of the sum of loads. Data captured includes number of overloads; number of weight cycling and accumulated total weight; register of the last 1,000 overloads with maximum weight, start date, time and duration; register of the last 10 weighings with maximum weight, start date and time; and estimates of the working group with number of cycles and maximum weight over time.
Dunville said: “In simple terms, the Eagle limits the hoist from picking up too much. But it can also control no-fly zones, where perhaps a section of runway isn’t rated as high as another or a customer doesn’t want a load carried near a particular machine. For example, if a crane loaded with a coil raised all the way up extends 10 ft. below the girder but the empty hoist only extends 5 ft. below the girder, that difference may cause contact with expensive plant fixtures and machinery. We can limit the crane to only travel in that area when unloaded or to completely nil travel in that area.”
He added: “We typically work with crane manufacturing and service companies or hoist OEMs [original equipment manufacturers], but we will work with end users upon request. Importantly, we are crane people only selling crane solutions; we don’t do other applications. We manufacture and assemble everything at our facility and test it as a system to ensure those in the field don’t have to do on-the-job integration. When there are problems, people can talk to experienced crane people at our offices in Spanish or English.”