Creform Custom AGV
Creform Corporation has designed and built a new custom AGV system utilizing its FH-B50066 bolt-on AGV drive, single-directional unit.
The system features two drive wheels–one located toward the front and a second toward the rear. Each end independently follows the guidepath for the accurate and consistent travel necessary for smooth conveyor transfers. The system was built for an automotive powertrain supplier and has detailed requirements necessary to support their process equipment for around the clock operation.
The AGV, part of a plant-wide use of Creform AGVs, and with overall dimensions of 67″ L x 38″ W x 70″ T, features a conveyor transfer height of 20 in.
The conveyor area is 31″ wide and 33″ across with 600 lb. capacity. The unit essentially acts as a transfer vehicle between conveyors at multiple manufacturing points and features one powered conveyor deck for automatic load transfers. Mechanical load safety-stops rotate down when pulling into the conveyor stations to allow transfers. Gravity causes them to rotate back up when leaving the transfer point to ensure that the load is secure.
It can travel at speeds up 50 M/min and along an approximate 100 ft. long magnetic tape guide. Floor positioned RFID tags are used for the control of speed and obstacle sensor views.
Photocells on the AGV’s conveyor deck are used for load control functions and serve to verify that the load is secure during travel, as well as used for slow-down and stop functions. Any load shift is detected and will stop the AGV. Optical communication devices coordinate the conveyor operation between the AGV and stationary conveyor units. It features radio communication to interface with the traffic management system to keep the system moving efficiently.
The AGV features a heavy-duty fabricated steel base for strength and rigidity. Forklift tubes are integrated into the frame’s design which allows easy and safe lifting for maintenance.
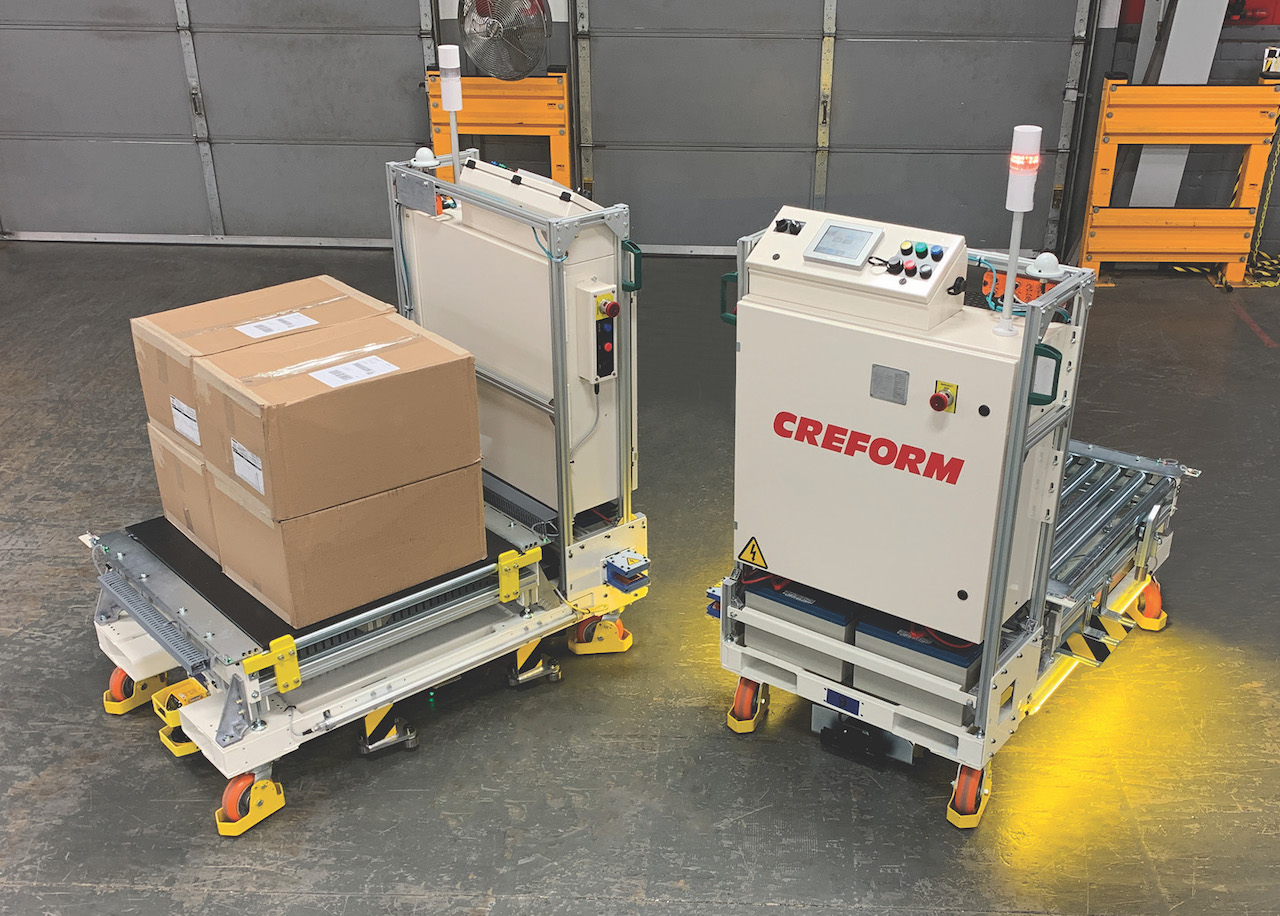
Creform AGV with single conveyor deck.
The unit incorporates a 24-volt system, powered by two 12V AGM batteries with easy access under the control panel. The opportunity charging system, activated by photocells, minimizes need for the user to manually change batteries. With each circuit of the guidepath, batteries are automatically charged by just pulling into the charging station positioned along the route. No human intervention is necessary.
Safety category 3 features on the AGV includes a safety circuit to cut power, audible warning device, flashing light, E-stops, LED light band along both sides of the AGV and a laser scanner on the front of the AGV. An HMI touch screen is used for user and maintenance interface with an operator screen positioned at the top of the AGV control box.
The Creform system is used to create an array of material handling and efficiency enhancing devices and is a proven component in continuous improvement and Lean Manufacturing programs. The company partners with customers in developing and implementing these programs.