RobotWorx, OCTOPUZ Robot Programming
RobotWorx, an Ohio-based industrial robotic solutions and customized integration company has entered a strategic partnership with OCTOPUZ Inc.
The new collaboration will allow RobotWorx to expand its service offerings into offline robot programming with a leading software creator. While traditional robotic programming requires downtime and manual manipulation of a teach pendant, OCTOPUZ provides a better solution. OCTOPUZ enables path-sensitive, complex robot applications to be programmed without disruption to the manufacturing process.
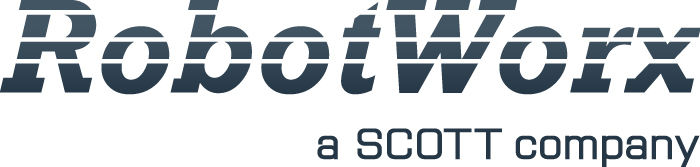
RobotWorx is an industrial robotic solutions and customized integration company.
How it Works
Users create detailed virtual simulations of their real-world robot cells, complete with machinery and manufacturing components, in minutes. Within this virtual cell, OCTOPUZ uses built-in machine logic to automatically identify the optimal toolpath trajectory and program the required code for a multitude of industrial tasks. The code is then accurately converted to the robot brand’s unique language for use in the real world.
OCTOPUZ removes the traditional limitations of robot automation by enabling robot programming to be completed virtually, on a computer, while the robots are still online and working for you.
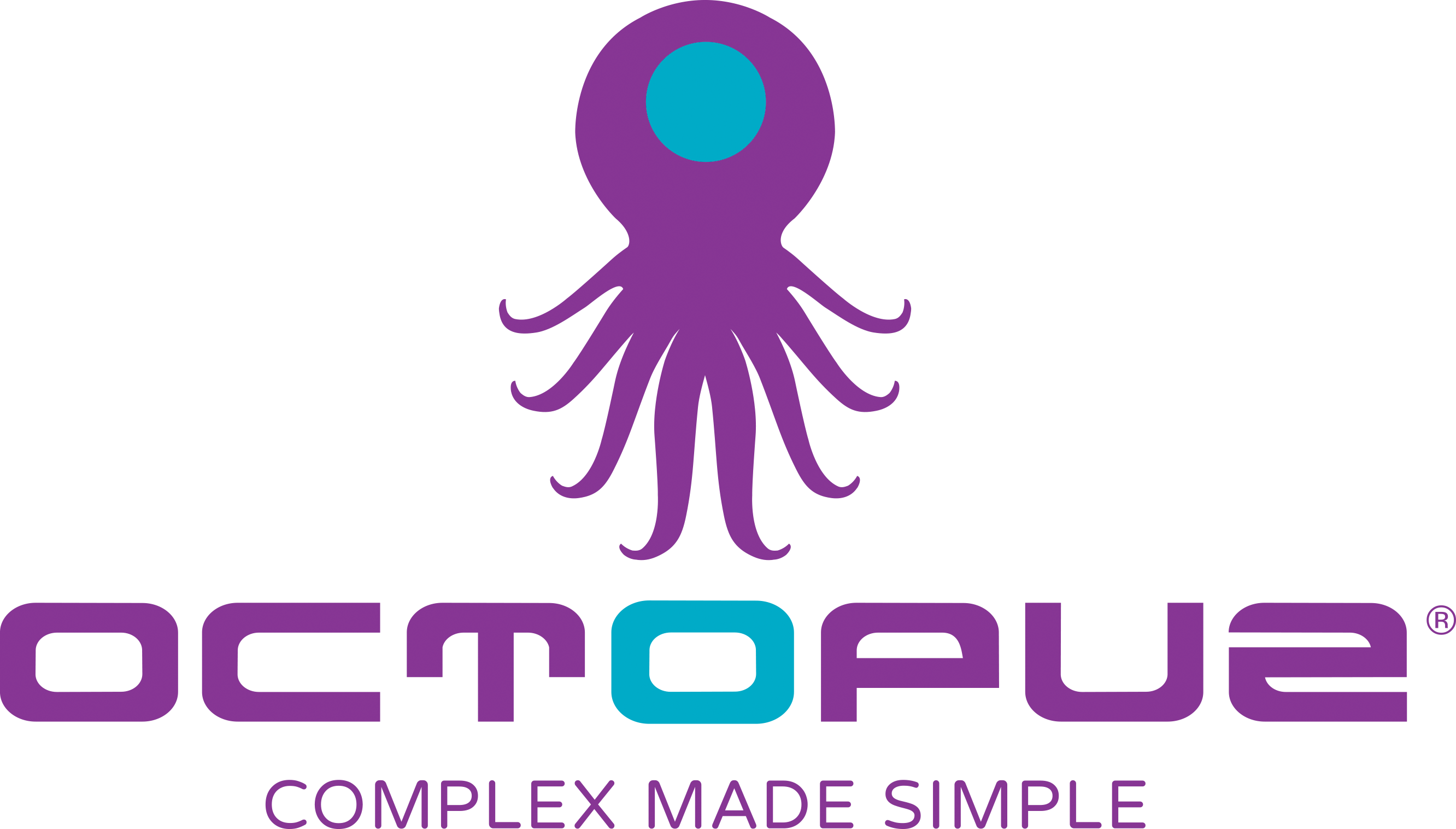
OCTOPUZ enables path-sensitive, complex robot applications to be programmed without disruption to the manufacturing process.
Maximize Robot ROI
RobotWorx is excited to provide this new solution to its existing and new customers with several benefits:
- Simplify toolpath programming – An Intuitive, user-friendly software interface enables non-experts to confidently program complex robot applications. Program through import from CAD or CAM software or natively in OCTOPUZ.
- Automatically detect and avoid errors – Quickly resolve potential toolpath errors including singularities, joint limits, reach limits, and collisions.
- Validate robotic processes through simulation – Ensure the robot will perform tasks as expected through start-to-finish simulation.
- Program and post multi-robot cells – Program, simulate, and generate code for multiple robots in a single cell.
- Single platform for all robot brands – Extensive component library with support for many robot brands in any configuration.
- Support for all robot manufacturing processes – Support for welding, machining, cutting, spraying, additive, and everything in between.
- Reduce production downtime – Reprogram new robot functions in hours rather than days, without ever taking the robot offline.