SEAA Projects of the Year
The Steel Erectors Association of America (SEAA) announces the winners of its 2024 Projects of the Year. Two companies were recognized for Miscellaneous Metals and three for Structural Steel projects.
Projects that were topped out in 2022 or 2023 were eligible and must have been completed without significant accident or injury. Submissions are reviewed and winners are selected by an independent panel of judges from an engineering firm not affiliated with the association.
“Only one of the five winning companies is a prior recipient of this award, and two of them are relatively new members of SEAA,” said Drew Heron, Chairman of the Awards Committee. “Regardless of the size or scope, each of these projects demonstrated the grit and talent it takes to be an ironworker,” he said.
Winners receive trophies, feature article coverage in Connector magazine, and the chance to participate in peer panel discussions. Summaries provided below.
Miscellaneous Metals Class II (up to $500,000)
In Atlanta, Georgia, Porter Steel, Inc., had to deliver materials for an 8,625 lb AESS staircase to be installed between 9th and 10th floors of an office building using a 5 ft x 8 ft elevator. The VISA office staircase started in Porter Steel’s fab shop, Lilburn, Georgia, where the stairs were fabricated in five sections. Each section weighed between 1,366 and 2,140 lbs. Each section had to be rolled into the building on carts, then transported in a freight elevator measuring just 5 ft x 8 ft. Each section was rigged and welded on site.
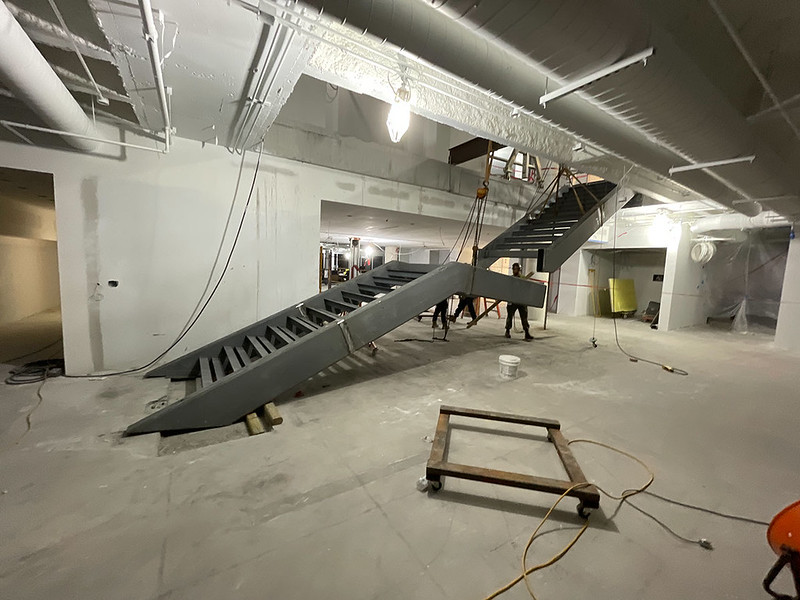
The VISA office staircase started in Porter Steel’s fab shop, Lilburn, Georgia, where the stairs were fabricated in five sections.
The focus for the erection team was on managing the weight, size, and logistics to make installation possible in the restricted space.
Miscellaneous Metals Class II (over $500,000)
All Things Metal faced setting structural steel by hand in the basement and upper floors of a 100-year-old building conversion into a posh boutique hotel. Located in downtown Phoenix, Arizona, the building was hemmed in on one side by a light rail line.
The Luhr’s Moxy Hotel project demanded a delicate balance between preserving the building’s rich heritage and implementing modern upgrades. Getting steel inside the building and erecting it in the basement and upper floors of the building proved the most challenging aspect of this job, which was compounded by navigating unforeseen structural issues. The building’s foundation, materials, and architectural nuances, reflective of a bygone era, demanded a thorough understanding to ensure that any modifications seamlessly integrated with the original design.
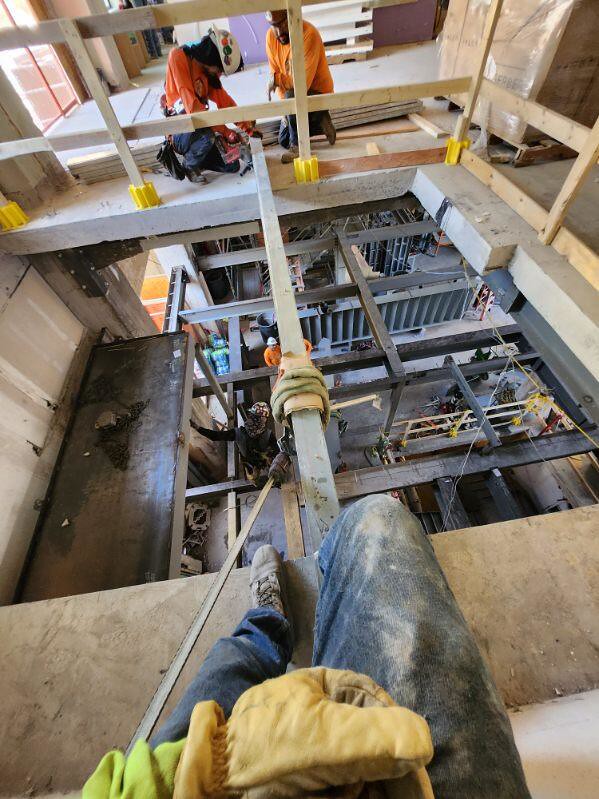
All Things Metal faced setting structural steel by hand in the basement and upper floors of a 100-year-old building conversion into a posh boutique hotel.
Structural Class II ($500,000 to $1 Million)
Kentucky based Cumberland Steel Company faced similar site access difficulties building an immersive sports, entertainment and arts venue in The Colony, Texas. The COSM Grandscape features an 87 ft diameter LED dome. When construction began it was only the second structure of its kind, and it was being built at the same time as the other. Without the benefit of hindsight for engineers and the fabricator, the primary challenge for Cumberland Steel Company was responding in real-time to constant design changes.
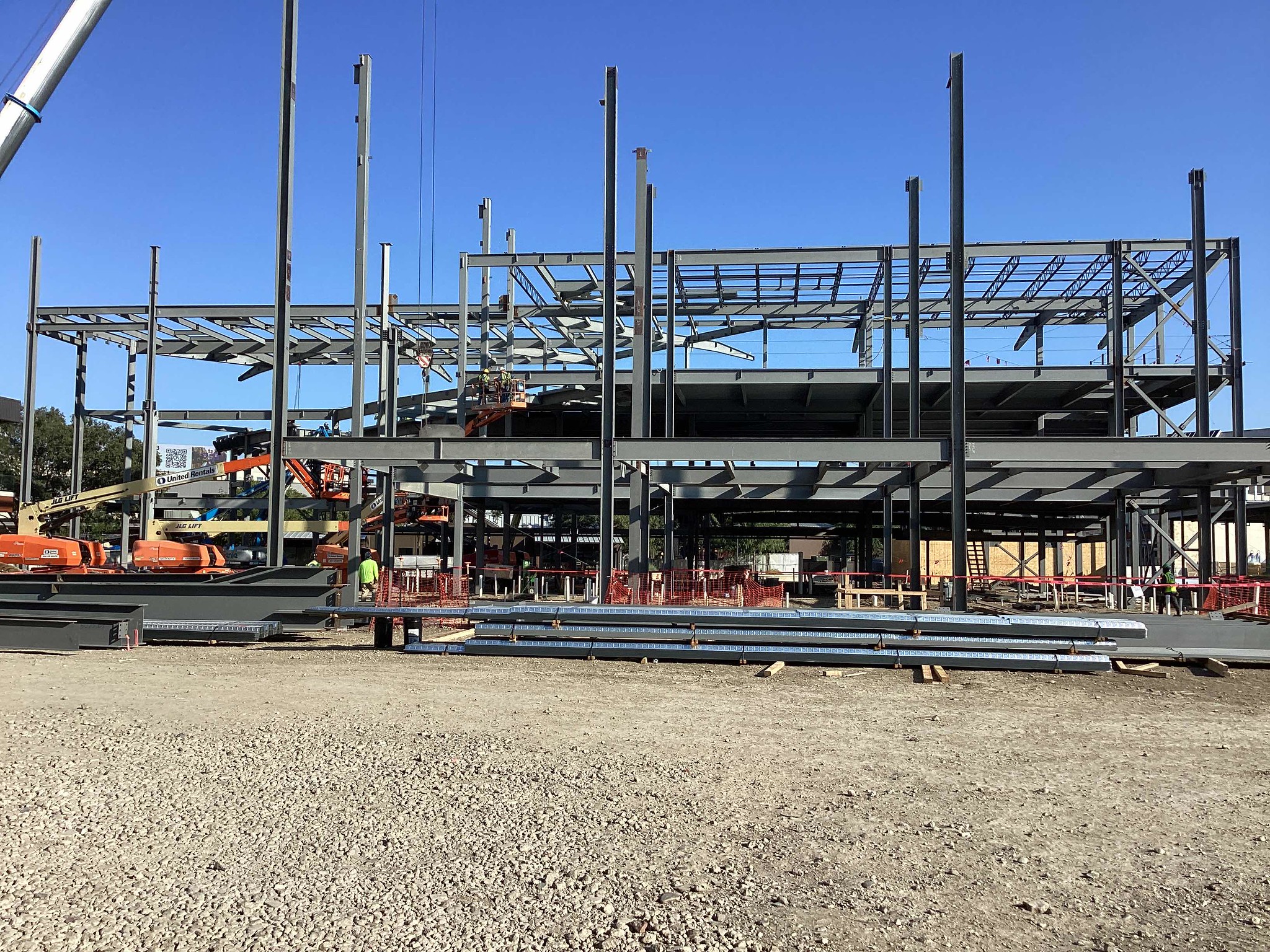
Kentucky based Cumberland Steel Company faced site access difficulties building an immersive sports, entertainment and arts venue in The Colony, Texas.
Daily surveys, constant communication, and flexible manpower enabled them to adjust to sequencing changes, and ultimately the job was completed without any fit-up issues.
Structural Class III ($1 Million to $2.5 Million)
On the campus of High Point University in North Carolina, D.S. Duggins Welding, Inc., based in Winston-Salem, faced the usual challenges of a tight job site and even tighter delivery schedule. But the real conundrum was solving problems with columns pulling out of tolerance after being set, tied in, decking placed, and concrete poured.
Although the columns were confirmed to be within AISC tolerance before turning the section over, they later moved outside of allowed tolerance once slab on decks were poured. While no root cause with the concrete pour or design was ever determined, the D.S. Duggins Welding team did what they had to make the building right—spending many hours and six figures in labor and equipment to resolve the problem. At the heart of the campus, the new five-story Panther Commons now serves as residence hall, retail, dining, and study space for students.
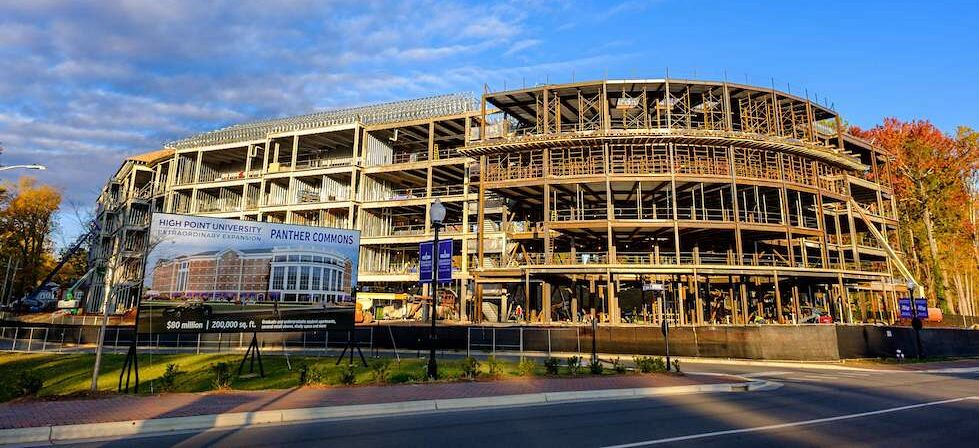
On the campus of High Point University in North Carolina, D.S. Duggins Welding, Inc., based in Winston-Salem, faced the usual challenges of a tight job site and even tighter delivery schedule.
Structural Class IV (Over $2.5 Million)
At Cape Canaveral Space Force Base, Launch Complex 36 is home to Blue Origin’s new Glenn rocket, which marks a pivotal milestone for U.S. space exploration. This complex is the first ground-up construction at Kennedy Space Center in more than 50 years. The steel erection contract was valued at more than $46 million.
Harrisburg, Pennsylvania-based S&R Enterprises is no rookie when it comes to big government projects and is the only repeat winner this year. The project included two 633 ft tall towers and assembly of a massive hydraulic pit. In all, 15 modules were constructed and stacked on top of each other. One module was lifted more than 600 feet high. The heaviest module, weighing 1 million pounds, had to be crawled about 100 feet into position using a unique crane configuration.
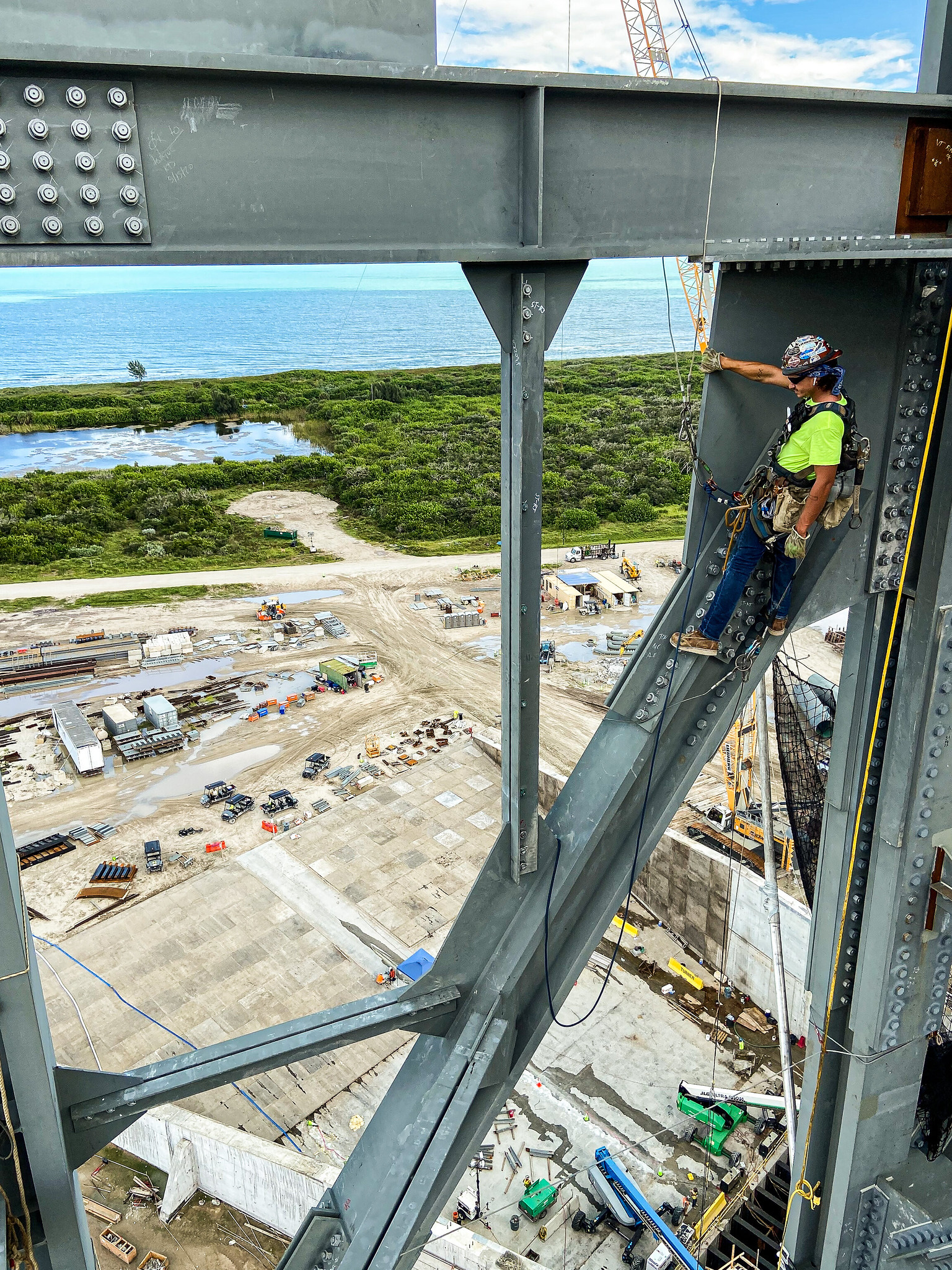
Harrisburg, Pennsylvania-based S&R Enterprises is no rookie when it comes to big government projects.
The scale and complexity of this project required coordination of multiple crews, modular construction techniques so that all trades were used as efficiently as possible, and around the clock schedules in order to meet strict launch deadlines.