Spot the Solution
A 2022 pilot proved to officials at Dominion Energy that Spot can help improve efficiency and boost worker safety.
Dominion Energy, which is headquartered in Richmond, Virginia and provides power to 7 million customers across 13 states, has experimented for years with using robotics to assist with routine inspections and respond to potential safety hazards.
Even though officials at the organization recognized the potential for robots to improve employee efficiency and keep human workers out of harm’s way, previous attempts to incorporate robotics have run up against significant limitations. One crawling robot was physically tethered to its controller, limiting the areas it could explore and requiring a human operator to accompany it at all times. Drones were more flexible, but they were hampered both by restrictive weight limitations and by batteries that sometimes fully drained in as little as ten minutes.
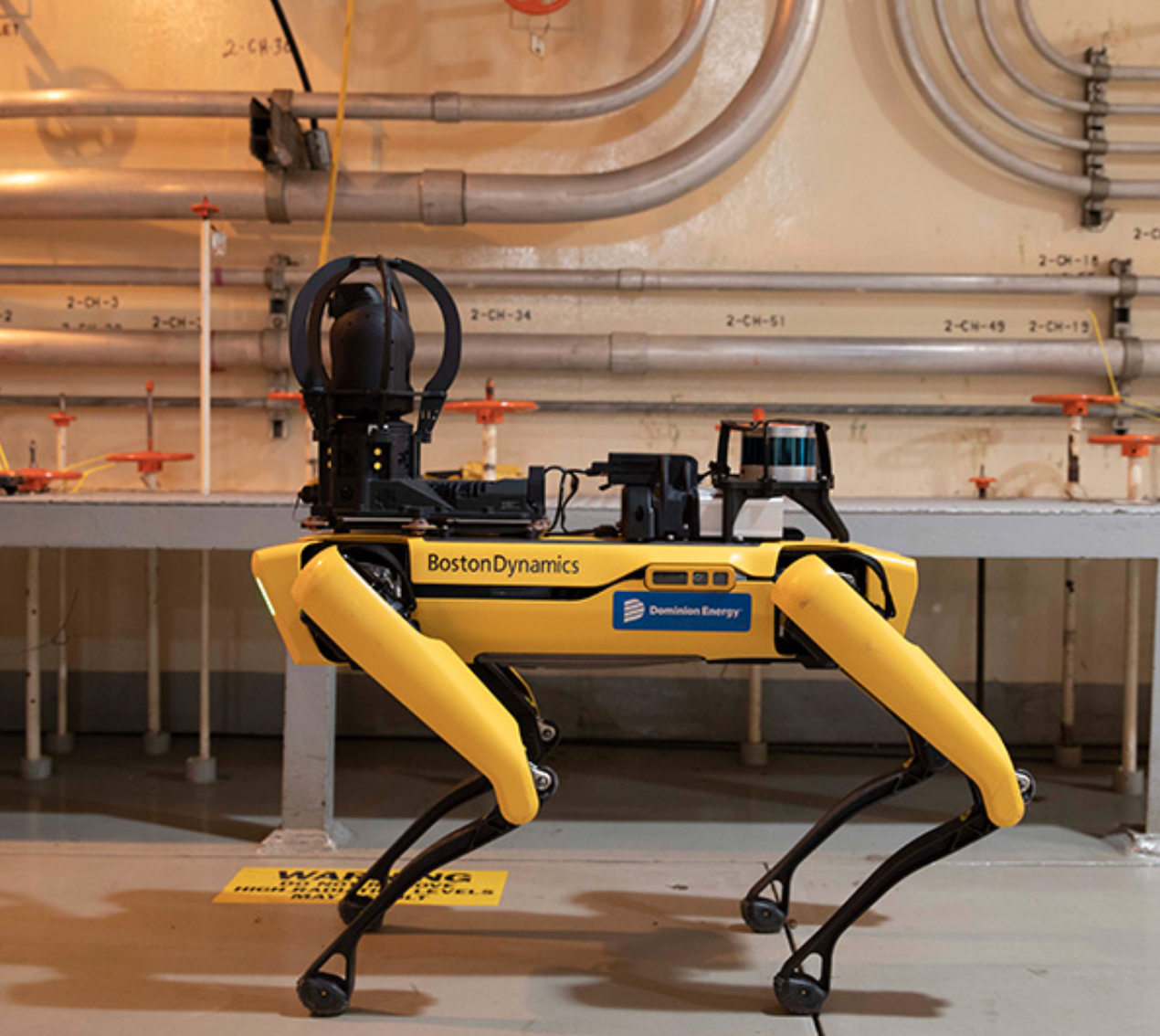
Dominion technicians attended a Spot training where they learned how to set up inspection routes for the pilot program.
After connecting with Boston Dynamics at a virtual robotics conference, the Dominion team immediately recognized the potential of the quadruped robot Spot to overcome these challenges.
“We’ve been exploring the value of robotics for data gathering and inspections for at least two and a half years,” says Joshua Bell, a nuclear technology and innovation consultant for Dominion. He continues: Spot’s 90-minute battery life was a huge selling point for us. We can get the robot to a site and do a full job, because that’s a normal duration for most work activities.
We see a lot of value in a robot being the first eyes on any sort of inspection location, for safety reasons. The more we know about a location before we send in a human worker, the better prepared we can be.
“When we saw that Spot was an alternative that doesn’t have the same flight issues as a drone, we recognized immediate possibilities,” says Marc Fischer, a health physics technician for Dominion.
Fischer’s role involves employee protection against radiation exposure — an area where Dominion and other energy companies see robots playing a large role in the near future. “Any time you’re in a radiation area, and you don’t have to send in a person, it benefits the long-term health of employees,” Fischer says. “That’s a tremendous help.”
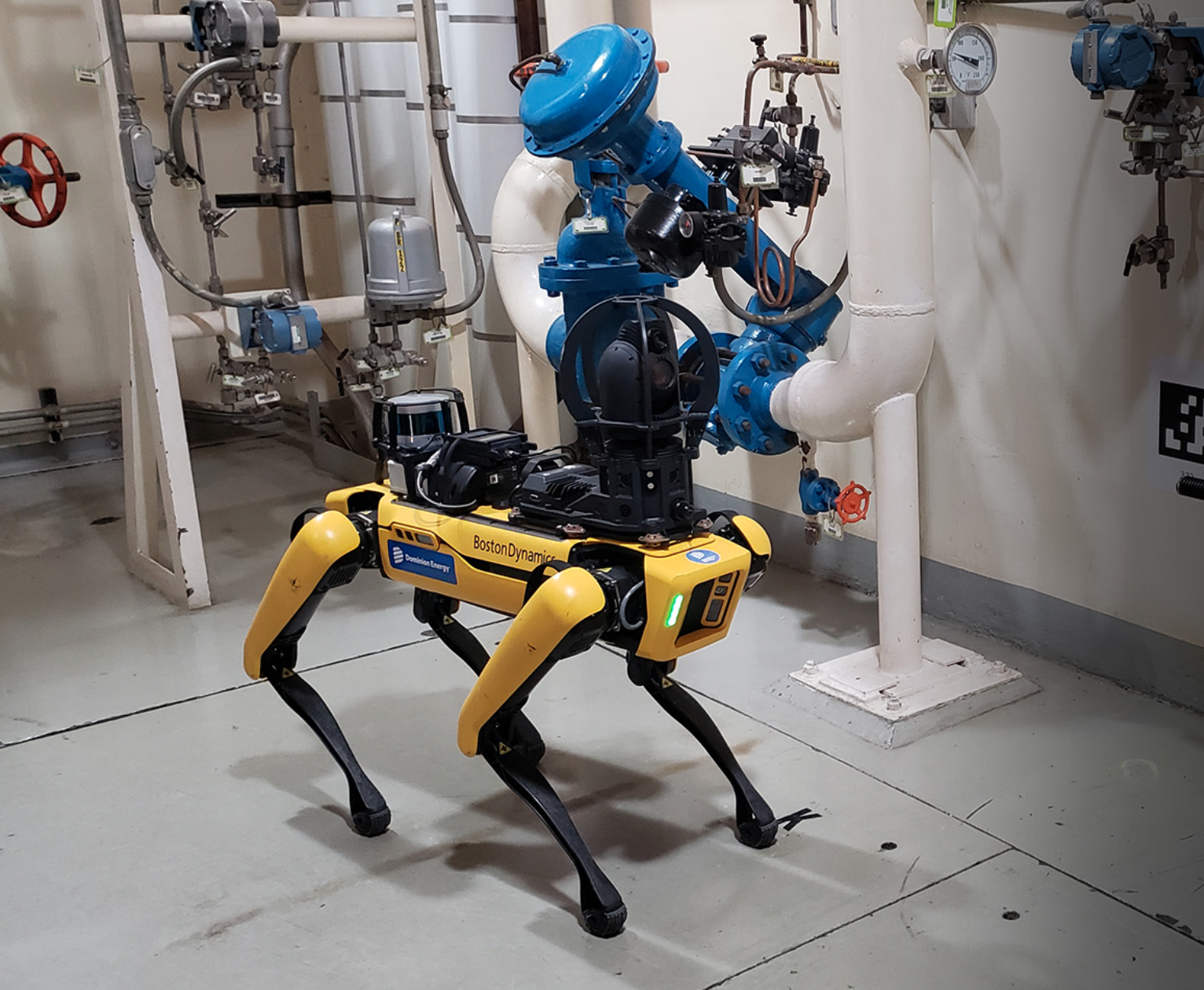
The pilot showed that Spot was not only able to conduct the same radiation surveys as human workers, but also that the robot actually obtained more consistent data.
Getting Started
Dominion received Spot in the fall of 2021, and officials initially brought the robot to several sites for demonstrations, where they gathered information from employees about how the robot might help them complete their day-to-day tasks. Officials spent two months planning a testing program, and then in February of 2022, they kicked off a pilot at the Surry Nuclear Power Station, which is located in Surry County, Virginia and provides power to 420,000 homes.
Officials wanted to start off with the predictable, repeatable task of site radiation surveys. In the existing workflow, employees would walk through a space holding a radiation detector, take readings at set intervals, and write down their findings. Then, they would return to their offices and enter the data from their handwritten notes into software to create a digital radiation map. The process is necessary for setting guidelines on what sorts of protective gear workers need to wear in different areas of the plant, and to detect any abnormalities.
Because Spot’s controls are so intuitive, Bell says, workers were able to get the pilot project up and running after just a very brief training session. “Everyone who has operated Spot picked up the controls and seemed comfortable within 15 minutes,” he says. “And then with the collision avoidance, we were able to comfortably navigate the robot without hitting any equipment. That feature is another huge part of why we’re comfortable moving forward with other pilots and exploring other use cases.”
Dante Piccolomini, a health physics technician at Dominion, says that operators spent just a couple of hours on a Friday getting used to Spot’s controls, packed the robot up for the weekend, and then got started with the pilot program the following Monday morning. They quickly moved from using the driver controls to supervised autonomous runs with the robot, and then conducted fully autonomous, unsupervised runs.
“I would just hit the ‘go’ button, and then Spot would go out and do the entire mission by itself,” Piccolomini says. “I didn’t have to be within a certain distance. There were no restrictions. And Spot did everything we would expect it to do.”
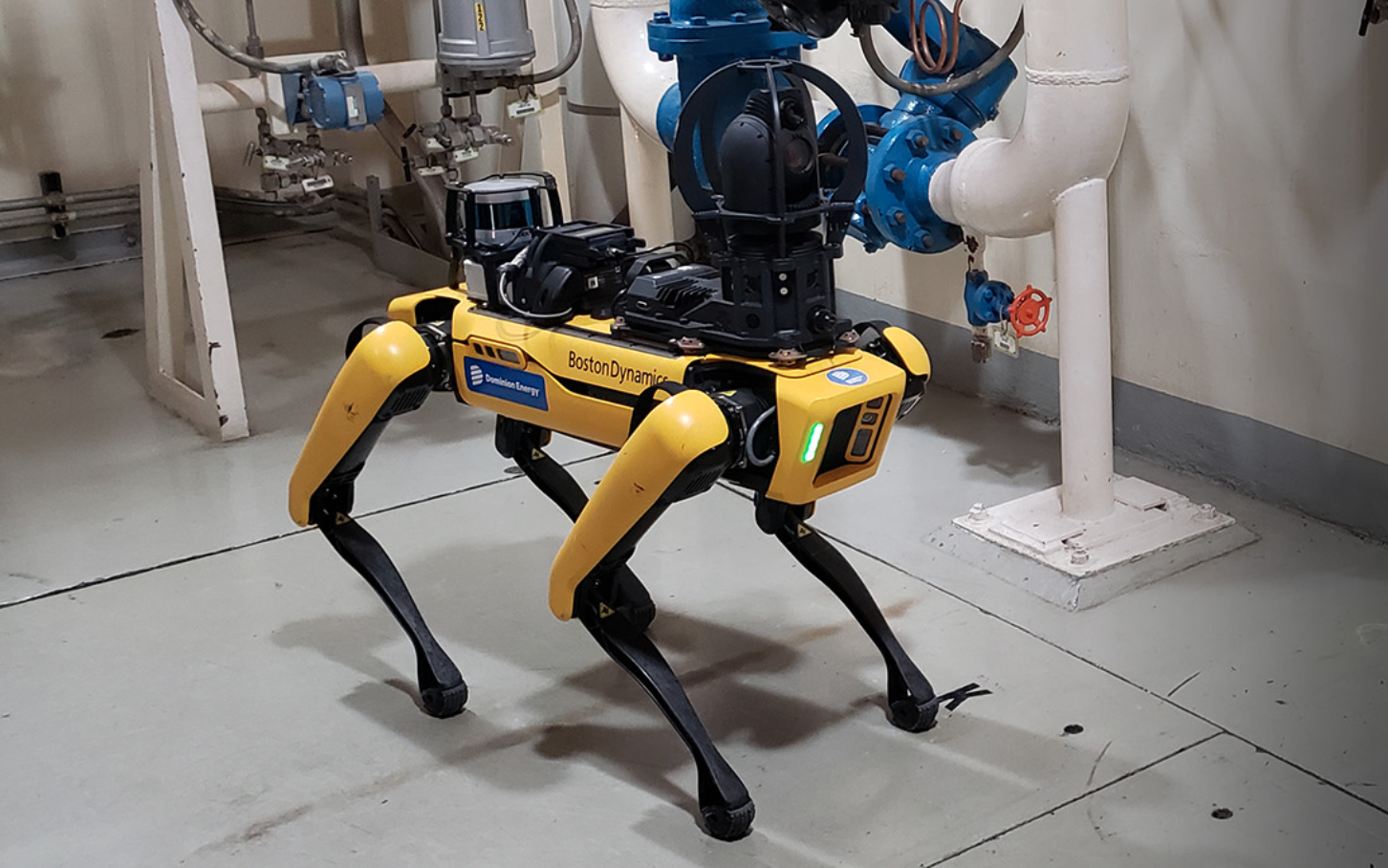
Dominion officials see vast potential for Spot to limit radiation exposure for employees.
Pinpoint Precision
The pilot showed that Spot was not only able to conduct the same radiation surveys as human workers, but also that the robot actually obtained more consistent data. “The robot took the radiation reading in the same place, with the same orientation, every time,” says Fischer. “So, it was getting more consistent numbers than we actually get. But Spot was doing those same readings every day in the same place, and as a result, the data was very consistent and very precise.”
That sort of repeatability and precision is key for inspections, where only a slight change in metrics might signal the very beginning of a potentially dangerous problem, says Piccolomini. “Because Spot is able to go out every week and follow along the same route and get those readings at the same points, we can track data and find trends. That can help us find issues with the plant, and possibly even prevent problems before they happen.”
Based on the pilot, Dominion officials see vast potential for Spot to limit radiation exposure for employees, both through regular inspections and through crisis response. “We do have radiation exposure goals, and meeting those goals has significant implications for our employees, insurers, and for our performance,” Bell says.
Bell notes that U.S. workers are allowed to receive a maximum dose of 5 rem per year on the job, and Dominion’s limit is even lower, at 3 rem per year. (For comparison, a full-body CT scan exposes a person to around 1 rem.) Then, there are also radiation limits for individual tasks. While workers need to take the precaution of donning protective gear or standing behind walls to limit their exposure, Bell notes that Spot can complete some tasks faster because it does not need to go through these additional steps. “The robot definitely received far more dose than the operator would have to gather the same kind of information,” he says.
Working with Boston Dynamics
Early on, Dominion technicians attended a Spot training where they learned how to set up inspection routes for the pilot program. They also learned how to pull data from the robot to share back to Boston Dynamics, a process that Bell says has been invaluable for troubleshooting.
In one part of the Surry plant, there is a maze-like entrance that helps with radiation shielding. The narrow, 90 degree turn with no landing on either side is designed to mitigate radiation exposure. Typically, Spot was able to make it through the entrance without assistance, but there were times when the robot got stuck, and workers couldn’t figure out why. “Our operators could manually override and navigate the robot out,” Bell says. “But then we started sharing out data from the robot, and the team at Boston Dynamics helped us determine why the robot wasn’t able to immediately complete the mission in certain cases.”
“There were moments like that throughout, where we had a lot of support with pulling the data and sharing information so that we could get the most out of the robot — both for the success of our pilot, and the growth of robotics in an industrial environment,” Bell adds.
“That team was helpful throughout and fantastic to work with. Part of our enthusiasm was about how great the customer service was throughout the entire process, because we knew we could be comfortable depending on Boston Dynamics to support us in our next pilot.”
Looking Ahead
Now that Dominion has demonstrated Spot’s value in low-radiation areas, officials plan to start exploring uses in areas with higher levels of radiation. “It was really a successful pilot, and it opened up a whole range of new possibilities,” Bell says.
Fischer says he doesn’t think it will take long for Spot to become a routine part of Dominion’s operations. “Where I’d like to see it go is for Spot to walk around the building and not only take radiation levels, but also take vibration readings and temperature readings, and conduct contamination surveys,” he says. “It’s just a matter of getting the right sensors and doing the right programming.”
When Dominion officials are working with Spot, Piccolomini says, it’s common for other employees to approach the team with ideas for additional use cases. “People will come up to us and say, ‘Oh, can it do this?’ Or, ‘It’d be cool if we could have Spot do that.’ So, people are always thinking of ways to use Spot in their specific job fields. The more exposure they get to Spot around the worksite, and the more we use Spot in the field, the more we’re going to stimulate those types of new ideas.”