Warranty Enquiry Leads to Crosby Rigging Overhaul
The Crosby Group has completed training and overhauled rigging best practices at an end user’s facility where problems were encountered due to shock loading of a Crosby IP vertical lifting clamp.
Strategic distribution partner, B.C. Wire Rope & Rigging, which delivers heavy lifting services throughout California, Arizona, and Nevada, contacted Crosby when a customer had broken a cam segment in a plate clamp. The rigging component, suited to vertical lifting, turning, and transfer, was being used with a forklift truck to lift domes during a manufacturing process related to tank heads and accessories.
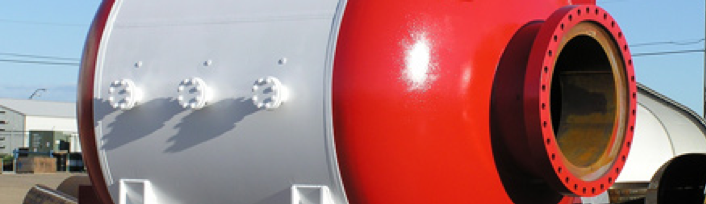
The clamp was being used with a forklift truck to lift domes during a manufacturing process related to tank heads and accessories.
Initially, the user’s enquiry centered on a possible warranty replacement, but subsequent dialog resulted in a more holistic solution than a simple part replacement. Regardless, the item would not have been covered by the warranty terms as it emerged that side loading, which equates to improper rigging, had caused the damage.
Jim DuCharme, district sales manager and product trainer at Crosby, said: “Having been invited to the site and viewed operating processes, it was apparent that both shock and side loading of the clamp had taken place. Upon completion of the initial walk-through the end user was receptive to expert guidance as to how working and rigging practices could be improved, not only with safety in mind but also to enhance productivity, while extending clamp and other product life.”
DuCharme suggested that Crosby lead a rigging training course at the facility, which resulted in two sessions being delivered to all workshop employees. Both classes lasted the best part of five hours and proved successful in imparting valuable education to the workforce. Content covered general safe rigging techniques and tailored information for the manufacturing processes at that particular place of work.
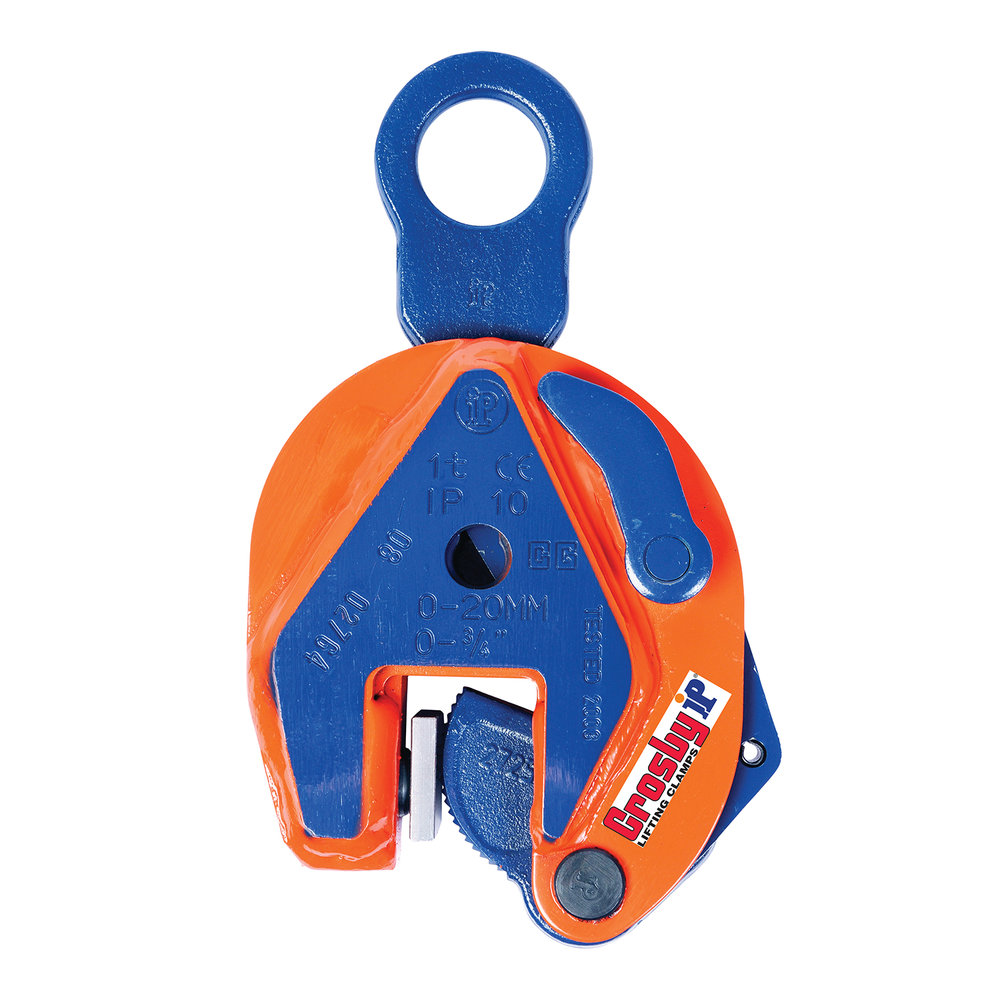
A Crosby IP vertical lifting clamp.
DuCharme added: “It’s remarkable what can cascade down from a warranty replacement enquiry and this case study serves to remind industry of the importance of looking at the wider issues that could cause damage to rigging gear or loads. I had never led a class where attendees were so engaged and anxious to learn. Within a week of the sessions, the safety manager was placing orders to replace chain slings and has since taken delivery of additional clamps and repair kits.”
Interestingly, the end user has remained in communication with Crosby about utilizing the lifting and rigging hardware specialist’s expertise in further enhancing material handling operations at the site. DuCharme has engaged Crosby’s product support team in the process to lead feasibility studies and subsequent research and development, principally related to the creation of a custom lifting clamp for handling the aforementioned domes.
DuCharme concluded: “Sourcing the right product for the job and using it correctly are two key components in safe rigging. It was a pleasure to work with B.C. Wire Rope & Rigging’s customer; its staff should be applauded for showing such willingness to learn and enthusiasm for continued improvement of lifting and site-specific best practices.”