Zebra’s FITT Solution
Zebra Technologies Corporation confirmed that global manufacturer FITT has improved its supply chain processes, product traceability, and order status visibility with an easy-to-use Zebra warehouse mobility solution.
- Established in 1969 and headquartered in Vicenza, Italy, FITT has almost 1,000 employees worldwide across ten European production sites including seven in Italy as well as 13 logistics hubs and five subsidiaries.
An international leader in the production and development of highly innovative fluid management solutions for domestic, professional, and industrial applications, FITT exports to 87 countries globally.
Its network of production and logistics centres are strategically located throughout Europe to help guarantee business continuity and top service levels to big clients, large central structures, and private individuals.
Customer orders are dispatched within two working days with around 6,000 lorries leaving its Italian Fara Vicentino site annually, shipping to 42 European countries.
Following the implementation of a new SAP warehouse management system in certain areas of its business, FITT needed a modern solution for its new processes and unified management system. Also, warehouse operators were using older mobile devices with small screens that were not wirelessly connected, which impacted productivity and accuracy.
Zebra helped develop a warehouse mobility solution to streamline FITT’s processes, providing long-range scanning, strong Wi-Fi connectivity and clear outdoor readability. This enables efficient tracking of 15,000 pallets and better supply chain product visibility of its 700+ stock keeping units (SKUs), from finished production to dispatch.
“Our managers and operators like the new user-friendly, integrated, scalable, Android mobile devices with larger screens that can be managed remotely and deliver better visibility and management of our warehouse and yard operations,” said Loris Gallo, ICT manager and SAP migration project manager, FITT, Italy.
“With a big facility along with multiple workflows, pallets and SKUs to manage, it’s essential we have a solution to help ensure customers’ demands are met quickly and accurately.”
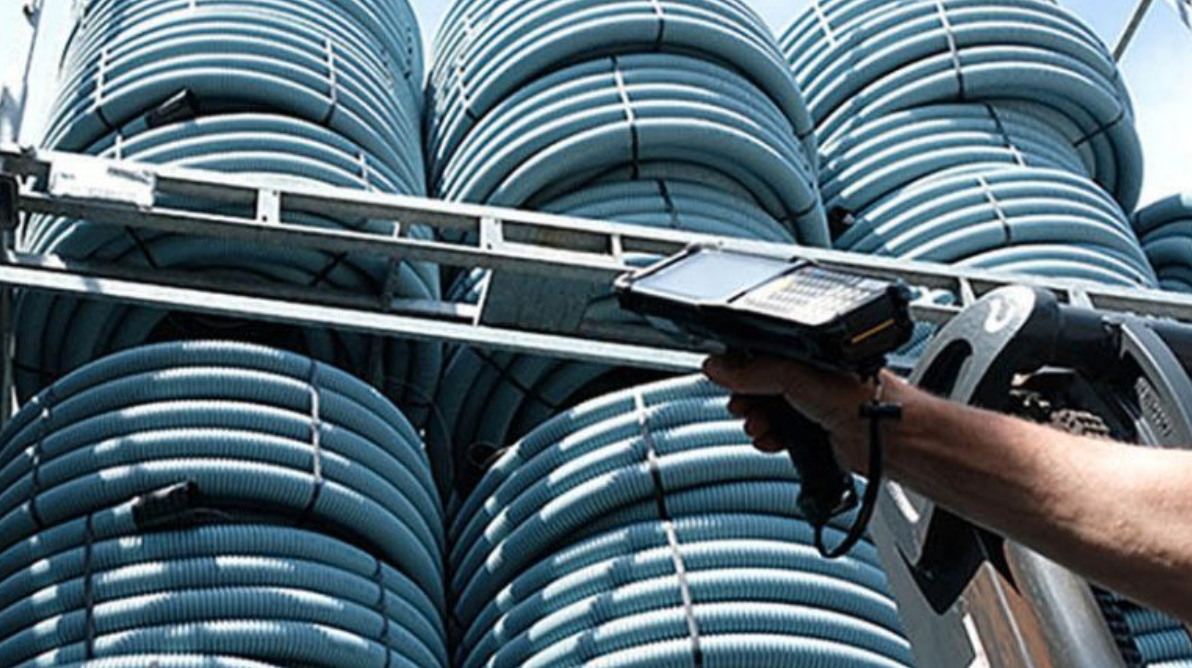
Zebra Technologies empowers organizations to thrive in the on-demand economy by making every front-line worker and asset at the edge visible, connected and fully optimized.
Zebra CC6000 customer concierge interactive wireless kiosks enable shift managers to accurately initialise, validate and cross check order production activities.
These devices help make teams more efficient and flexible, giving warehouse operators better control of production quality and outcomes. Warehouse teams use MC9300 ultra-rugged mobile touch Android computers in the 67,000 m² outdoor storage areas to manage inventory workflows, order picking, compiling pallets for dispatch and checking them onto lorries at one of the ten loading bays.
Workflow integration with SAP systems is supported by web-based interfaces and applications developed by FITT for finished product checks and inventory monitoring in-house, using the Zebra devices. The five-year Zebra OneCare service agreement helps optimise devices with relevant security patches, firmware and software updates, and timely repairs to help ensure peace of mind.
“Manufacturers need trusted advisors, and this collaboration including FITT and Zebra is a good example of what can be achieved with the right business insight and solutions,” said Enzo Tumminaro, director, Zebra Technologies Italy.
“Software integration with powerful, rugged, Wi-Fi scanning devices, and an understanding of front-line worker needs in the on-demand economy means FITT has a scalable, winning blueprint for its business now and in the future.”